The Single Minute Exchange of Dies (SMED) concept was developed by Shigeo Shingo, an industrial engineer at Toyota. It refers to the process of reducing the time required to change over a machine or production line from one product to another to under 10 minutes.
The primary goal of SMED is to do for faster changeovers, which increases flexibility, reduces downtime, lowers batch sizes, and supports just-in-time (JIT) production.
What is the SMED Principle?
The SMED principle is to eliminate waste. It promotes analyzing the changeover process to separate tasks that can be done while the machine is running from those that require the machine to be stopped. The SMED principle is to:
1. Convert as many internal activities to external as possible.
2. Simplify and streamline remaining internal activities to reduce downtime.
What is the SMED Tool used for?
The SMED tool is used to:
- Reduce setup times and improve machine utilization.
- Increase production flexibility by allowing smaller batch sizes.
- Support continuous improvement in manufacturing processes.
- Enable quicker response to market demands or product changes.
- This tool is commonly used in industries such as automotive, packaging, printing, and any setting where frequent changeovers occur.
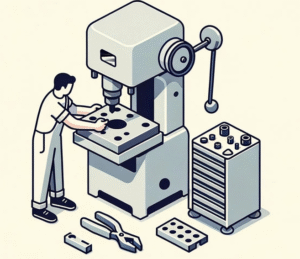
SMED Internal and External Activities
Internal activities:
Tasks that can only be performed when the machine is stopped (e.g., removing old dies, setting new dies).
External activities:
Tasks that can be done while the machine is still running (e.g., preparing tools, moving dies, tools and materials).
Note: The Purpose of SMED is to convert internal activities to external ones to reduce changeover time.
Single Minute Exchange of Dies Examples
Example 1: Stamping
- Before SMED: The Machine is stopped for 30 minutes while the operator retrieves press tools, prepares tools, and adjusts settings.
- After SMED: Tools and dies are prepared in advance, quick-release mechanisms are installed, and changeover time is reduced.
Example 2: Packaging Line
- Before SMED: 40-minute setup involving manual cleaning and adjustments.
- After SMED: Use of color-coded quick-change parts and parallel task execution reduces downtime.
Single Minute Exchange of Dies Formula
There isn’t a single SMED formula, but setup time can be broken down and analyzed using this structure:
Total Setup Time = Internal Setup Time + External Setup Time
For performance metrics, you can also use:
Setup Time Reduction (%) = [(Old Setup Time – New Setup Time) / Old Setup Time] × 100
Goal with SMED:
Reduce internal setup time by converting steps to external and optimizing remaining internal steps.
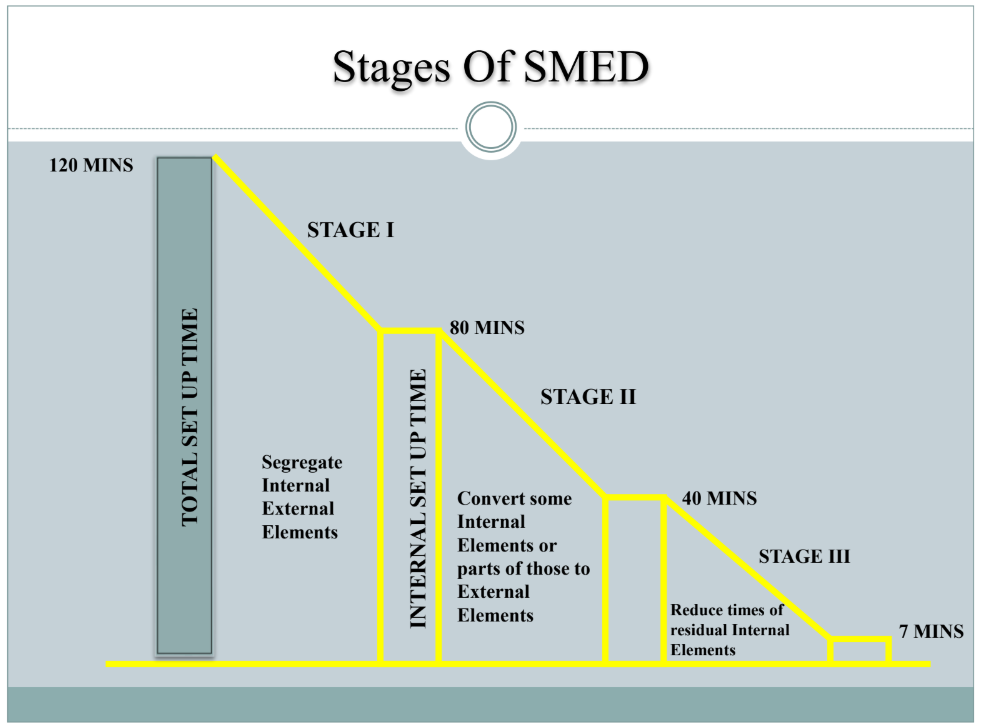
7 Steps of SMED
Implementing SMED follows a structured process. Here are the 7 steps of SMED:
1. Observe the current setup process: Record video or document every action during changeover.
2. Separate internal and external activities: Classify tasks based on whether the machine needs to stop.
3. Convert internal activities to external: Shift as many tasks as possible to ‘before/after the machine’ is stopped.
4. Streamline remaining internal activities: Use quick-release mechanisms, standardize tools, and reduce motion.
5. Streamline external activities: Organize workstations and pre-stage materials.
6. Document the new process: Prepare standardized work instructions.
7. Train and continuously improve: Monitor results and look for further improvement opportunities.
Benefits of SMED:
- Increases throughput by reducing setup times
- Eliminates setup errors
- Increases safety
- Reduces the cost of setups
- Reduces waiting times and inventory buildups
- Reduced setup time
Conclusion
The Single Minute Exchange of Dies is the main part of lean manufacturing. In SMED, setup times are reduced through a structured and systematic approach. SMED empowers organizations to operate more efficiently, respond quickly to changes, and reduce waste.
F1 Pit Stop Training:
You may like to read about other lean manufacturing tools: