Control Plan
The Control Plan in Quality is a documented description of the systems and the processes required for controlling the manufacturing of the product as per the IATF 16949 standard.
A control plan is the main document of the PPAP (Production Part Approval Process). The control plan covers all processes per PFD and PFMEA with a process number sequence. Now control plan is one of the core tools.
Types of control plan:
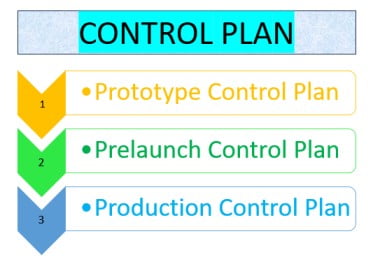
There are 3 types of control plans as per the phases of APQP.
- Prototype Control Plan
- Pre-launch Control Plan
- Production Control Plan
Prototype Control Plan:
It is the description of the dimensional measurements, material and performance test that will occur while preparing the prototype sample. Normally in a prototype control plan, all prototype parts are checked. Prototype parts are those that are made without complete tooling.
Pre-launch Control Plan:
It is a description of the dimensional measurements, material and performance test that starts after the prototype and before mass production. In the pre-launch control plan, parts are checked with a higher frequency than the production control plan for some critical parameters.
Production Control Plan:
It is the description of the Product and process characteristics, process control, test and measurement system that occur during mass production. In the production control plan, inspection frequency is normal as compared to the prelaunch control plan.
Input for preparing the Control Plan:
- Process Failure Mode and Effect Analysis (PFMEA)
- Process Flow Diagram (PFD)
- Lesson learned from a similar part/process
- Cross-functional team knowledge
- Drawing
- List of Machines
IATF 16949 Control Plan requirements:
8.5.1.1 Control Plan
The organization shall develop control plans at the system, subsystem, component and material level for the relevant manufacturing site and all products supplied, including those for processes producing bulk material as well as parts. Family control plans are acceptable for bulk material and similar parts using a common manufacturing process.
The organization shall have a control plan for prelaunch and production that shows linkage and incorporates information from the design risk analysis (if provided by the customer), process flow diagram and manufacturing process risk analysis outputs such as FMEA.
The organization shall, if required by the customer, provide measurement and conformity data collected during the execution of either the prelaunch or production control plans. The organization shall include in the control plan:
- controls used for the manufacturing process control, including verification of job set-ups
- First off/last off part validation as applicable
- Methods for monitoring of control exercised over special characteristics defined by both the customer and the organization
- The customer required information if any
- Specified reaction plan when a non-conforming product is detected, the process becomes statistically unstable or not statistically capable.
The organization shall review control plans and update as required, for any of the following:
- The organization determines that it has shipped non-conforming products to the customer
- When any change occurs affecting the product, the manufacturing process, measurement, logistics, supply sources, production volume changes or risk analysis (FMEA)
- After a customer complaint and the implementation of the associated corrective action when applicable
- At a set frequency based on a risk analysis
If required by the customer, the organization shall obtain customer approval after review or revision of the control plan.
Control Plan Format:
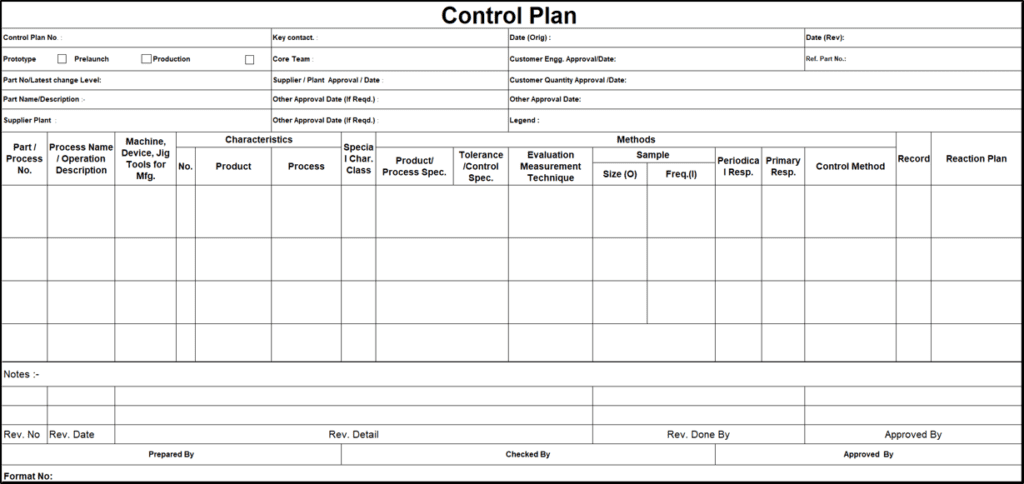
Control Plan Format in Excel:
Control Plan Header:
- Control plan number
- Effective date or Revision date
- Customer description
- Organization description
- Part description
- Part number/Latest change level
- Engineering change level
- Phase ( Prototype / pre-launch / Production )
- Key Contact person
- Process step
- Process description
Elements of the Control Plan:
- Control Plan Phase: Mark the type of control plan in the box, whether it is prototype, prelaunch or production.
- Control Plan Number: Provide the document number of the control plan as per the document number system.
- Part Number/Latest Change: Write the part number as mentioned in the drawing. Internal part numbers can be written here if any.
- Part Name/Description: Write the name or description of the part as mentioned in the drawing. But if the control plan is of the family of parts, then mention the family model name here.
- Supplier/Plant: Write the name of the company or plant where the production run
- Organization Code: Mention the organization code as provided by the customer
- Key Contact/Phone: Write the Name and contact number of the responsible person for the process
- Core Team: Write the name of the cross-functional team that was involved in preparing the control plan
- Supplier/Plant Approval Date: Write the document approval date by the customer
- Other Approval/Date: Write any additional approval information and date if required
- Date Original: Write the date when the control plan was initially developed
- Date/Rev: Write the latest revision date of the control plan
- Customer Engineering Approval/Date: Write the customer engineering approval date if required
- Customer Quality Approval/Date: Mention customer quality approval if required
- Other Approval/Date: Write any additional approval information and date if required
- Part/Process Number: Mention the process step as per the process flow diagram
- Process Name/Operation Description: Write the process name as mentioned in the process flow diagram
- Machine/Device/Jigs/Tool for Manufacturing: Write the equipment, machines, tools, fixtures, jigs etc required for the particular operation
- Product characteristics: Product characteristics are physical features of the part or assembly as mentioned in the part drawing.
- Process characteristics: Process characteristics are those features that are related to the process. For example, for a Mig welding process
- Special Characteristics: Write the defined symbol for the special characteristics in this column in front of the product and process characteristics as applicable.
- Product/Process Specification/Tolerance: Write here the product and process specifications with tolerance as per the drawing and process.
- Evaluation/Measurement technique: Write the relevant measuring instrument, gauge or testing equipment for the product and process. For example, appearance is checked visually and a dimension (diameter) is checked by a micrometer.
- Sample Size: Write the number of parts to be checked during the setup and in-process
- Inspection Frequency: Write the frequency after which sampling will be done. It may be 1 hour, 2 hours or 4 hours as per the requirement per shift. Also it can be at the start, mid and end.
- Responsibility: Primary responsibility for part and process inspection is mentioned in this column.
- Control method(Prevention/Detection): Write the record name that is used to control that parameter. for example, Setup Approval report, in-process inspection report, Final inspection report, error proofing, daily machine check sheet, tool history card etc
- Record: In this column, mention whether the record is to be kept or not.
- Reaction Plan: Write the applicable containment action and corrective action in the reaction plan column.
The control plan should be reviewed and updated periodically. The control plan is a living document.
Reference: IATF 16949 Standard
You may like to read about:
Hi, you have shared a good information. My query is whether this can be followed by sales and service industry too?
Thank you.
Thanks for your query.These control plans are for the manufacturing industry only. But control plan for service industry can be created.
I highly recommend ernestopro.com for anyone looking to implement effective control plans in quality management. Their comprehensive approach and detailed resources on different types of control plans, including IATF 16949 standards, make them an invaluable partner. The clarity in their format examples and input guidelines greatly simplify the process of preparing and understanding control plans. Trust ernestopro.com to enhance your quality control processes with expert support and insightful solutions.
Fabulous, what a blog it is! This weblog provides valuable
facts to us, keep it up.
What’s up Dear, are you really visiting this web page daily, if so then you will without doubt take nice
know-how.
Write more, thats all I have to say. Literally, it seems as though you relied on the video to make your point.
You definitely know what youre talking about, why waste your intelligence on just posting videos to your site when you could be giving us
something enlightening to read?
Hey there! I simply would like to offer you a big thumbs
up for the great information you have here on this post.
I’ll be coming back to your website for more soon.