There are 6 steps in the FMEA process as per VDA & AIAG. These 6 steps provide a systematic approach to failure mode and effect analysis.
- Scope Definition and Project Planning
- Structure Analysis
- Function Analysis
- Failure Analysis
- Risk Analysis
- Optimization
1. Scope Definition & Project Planning :
The purpose of the process scope definition is to decide what product/process to include/exclude for review in the PFMEA project. Below are the main objectives for defining the scope:
- Project identification
- Project Plan
- Define the boundary of the analysis
- Identify the lesson learning sheet.
During the scope definition PFMEA header should be filled as below:

2. Structure Analysis:
The purpose of process structure analysis is to identify and categorize the production system into
- Process Item
- Process Step
- Process Work Element.
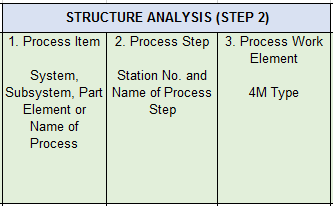
The main objective of Process structure analysis:
- System structure for a product or element of a process.
- Visualization of the scope of the analysis
- Identification of the process steps
- Basis for the function analysis steps
A Process flow diagram or Structure tree helps to define the process and provide the basis for structure analysis.
3. Function Analysis :
The purpose of the process function analysis is to ensure that the intended functions of the product/process are defined adequately.
The main objective of the function analysis :
- Check the functionality of the process
- Visualization of the process function using a process flow diagram.
- Association of characteristics to function
- Basis for failure analysis
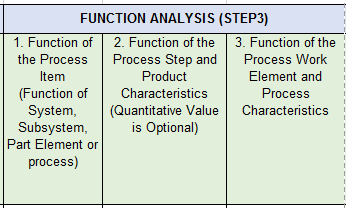
A function describes what the process item or process step is intended to do.
A requirement is related to the performance of the function and can be measured. Requirement falls into 2 categories :
- Product characteristics
- Process characteristics.
A product’s characteristics like geometry, material specification and surface finish etc. A process characteristic is shown on manufacturing operation standards or work instructions. A process characteristic like pressure, temperature, current, voltage etc.
4. Failure Analysis :
The purpose of the process failure analysis is to identify failure causes, modes and effects.
The main objective of the Process failure analysis :
- Establishment of the failure for each function of the process item
- Identification of the possible failure to process an element or step.
- Visualization of the failure relationship
- The effect may be shared by the customer with their supplier.
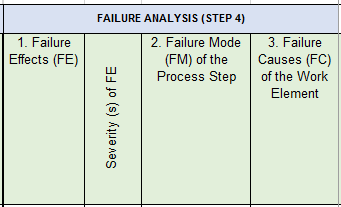
Failure of a process step is non-conformity to product or process characteristics. For a specific failure there are three categories:
- Failure effect
- Failure mode
- Failure cause
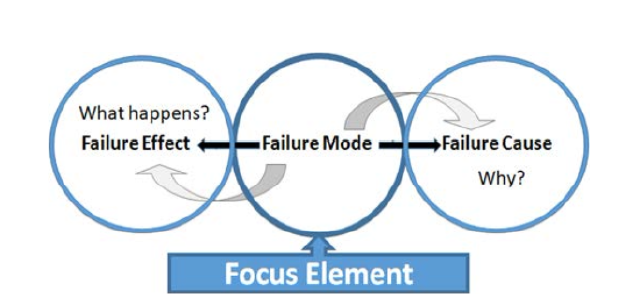
5. Risk Analysis :
The purpose of the risk analysis is to estimate risk by evaluating severity, occurrence and detection and prioritize the need for action.
The main objective of the risk analysis :
- Identify prevention control
- Identify detection control
- Rating of severity, occurrence and detection
- Communication between the customer and the supplier on the severity.
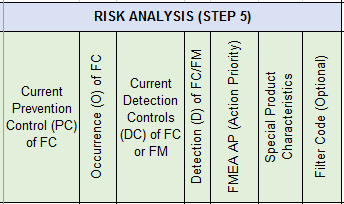
There are two different control groups :
- Current prevention control
- Current detection control
Action Priority (AP) :
In this new FMEA Action Priority (AP) replaced the RPN. The AP table provides the logic detail for the FMEA team for all 1000 combinations of S, O and D. It includes the logic-based description of each action priority level. There are 3 types of action priority in the AP table as below :
Priority High (H) :
The team must take or identify action to improve prevention or detection control. Or justify that the current control is OK.
Priority Medium (M) :
The team should take or identify action to improve prevention or detection control, or justify that the current control is OK.
Priority Low (L) :
There is a low priority for action. It means no need to take any action.
PFMEA Action Priority Table:
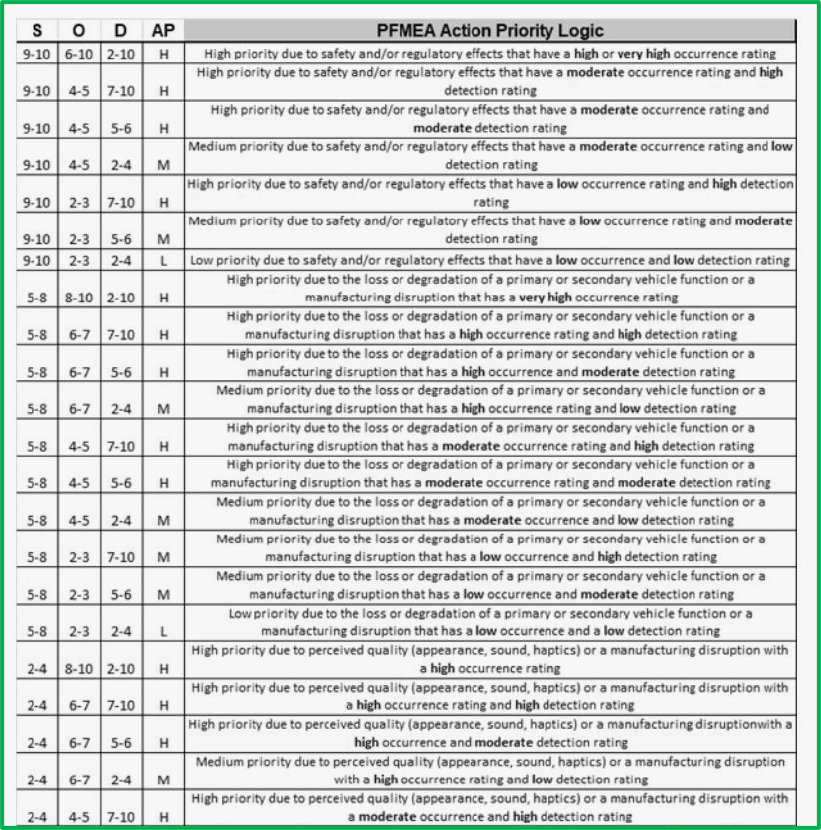
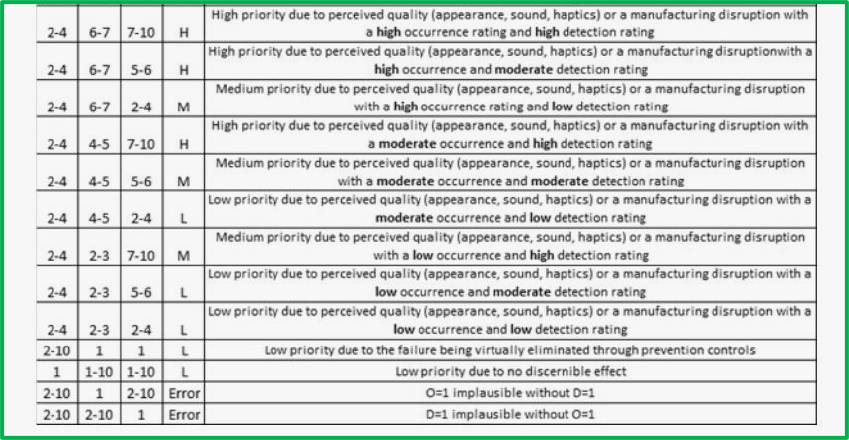
6. Optimization :
The purpose of the process optimization step is to determine actions to mitigate risk and assess the effectiveness of these actions.
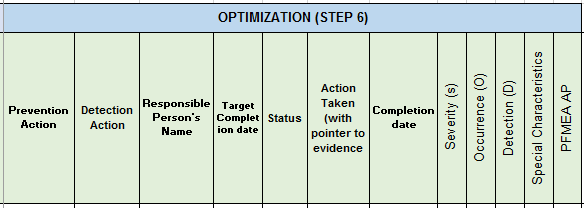
The main objective of the process optimization :
- Identification of the action necessary to reduce risk
- Assignment of the action and target completion time for action implementation
- Implementation and documentation of the action taken
- Confirmation of the effectiveness of the action taken
- Continuous improvement of the process
FMEA result documentation :
The scope and result of an FMEA should be summarized in a report. The report can be used for communication purposes within the company or with customers.
AIAG VDA FMEA FORMAT:
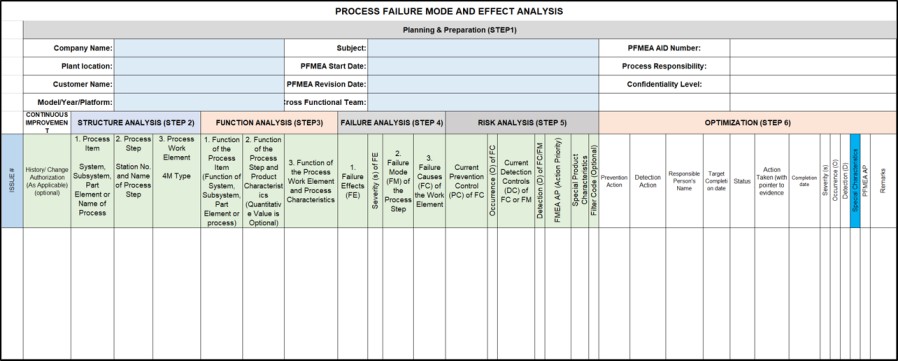
AIAG VDA FMEA Example:
Reference: AIAG VDA FMEA