Value Stream Mapping:
Value stream mapping is a method to check and improve the processes involved in delivering a product using flowcharts. The information and process flow from customer demand to delivery is examined by the VSM team. It is the main tool of lean manufacturing. Like other types of flowcharts, it uses a system of symbols to represent various processes and information flows.
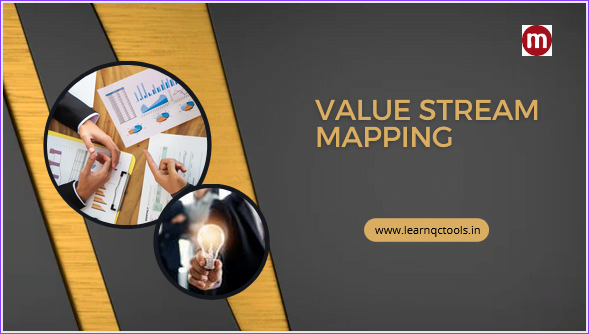
VSM is a very useful technique for finding and removing waste in processes from customer orders to dispatch. All processes are mapped as either value-adding or non-value-adding from the customer’s perspective. so that we can find the processes that do not add value.
It is very important to know that customers care more about the value of the parts to them than about the activities involved in producing them. Drawing a current state VSM and then preparing a better option with an ideal state and then a future state VSM is a standard technique.
Purpose of Value stream mapping:
- To check the current condition of the process.
- To identify the current gaps in the process.
- It helps to identify the process steps to focus on.
- To identify the waste from customer order to delivery.
- To improve the delivery to customers.
Why Value stream mapping is important?
- Normally the waste on your shop floor is visible. But value stream mapping makes it easier to identify the source of waste.
- Value stream mapping concentrates on both the material flow and the information flow, whereas many lean tools just concentrate on the material flow.
- By using VSM, you can identify waste and bottlenecks, plan for the future, and improve the quality of the finished product.
- Think about trying to construct a house without a blueprint. The Same is true in the manufacturing industry without value stream mapping.
Types of Value Stream Mapping:
Current State Map:
The current state map defines the steps to manufacture a product from customer order to delivery to the customer. It is the present status of all the processes to produce a product. To make improvements in the process, it is very important to understand the actual condition of the process at present.
Ideal State Map:
An ideal state map is the perfect condition of the process where there is no waste, no bottleneck and all customer requirements are considered. It is the situation that is actually the assumed condition by the VSM team so that a target for improvement can be decided.
Future State Map:
The future state map defines the process steps to make the product in the next few months. It is prepared to define the processes as per the ideal state map acquirement. The Future state map defines the current target and visualization of the processes to make a product in the future. There are some kaizen defined at this stage to achieve the future state map condition.
Steps for conducting Value Stream Mapping:
- Identify the parts to be studied and improved.
- Identify the problem for VSM for this part from the customer’s point of view.
- Identify the processes where value stream mapping will be done.
- Define the process steps for value stream mapping.
- Collect the current process data during mapping. e.g., cycle time, change over time, downtime, manpower & available time etc.
- Analyze the process steps to check the waste and bottleneck process.
- Map the movement of the product and information flow.
- Examine the inventory at each process to identify waste.
- Make a time plan. Check the processing time and lead time for inventory through all process steps.
- Analyze the value stream map to find out the waste.
- Prepare ideal and future state value stream maps.
- Prepare an implementation plan on the basis of the gap observed.