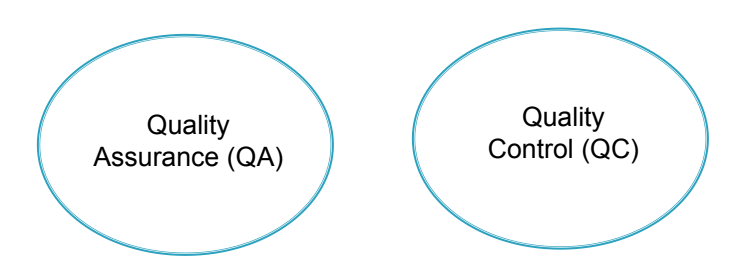
Quality Control:
Quality control is a process employed to ensure a certain level of quality in a product and process. It may include whatever actions an industry takes to provide for the control and verification of certain characteristics of a product and process. The basic goal of quality control is to ensure that the product meets specific requirements.
As per ISO 9001:2015 standard Clause 3.3.7,
Quality control is ” Part of quality management focused on fulfilling the quality requirement.”
Quality Assurance:
Quality assurance is the activity of providing evidence to establish confidence that quality requirements will be met. It also means assuring the customer that he can purchase a product with confidence. Quality assurance covers all activities from design, development, production, documentation, verification and validation. Quality assurance ensures do it right the first time.
As per ASQ, quality assurance is the planned and systematic activities implemented in a quality system so that the quality requirements for a product or service will be fulfilled.
As per ISO 9001:2015 standard Clause 3.3.6,
Quality Assurance is ” Part of quality management focused on providing that confidence that quality requirements will be fulfilled”
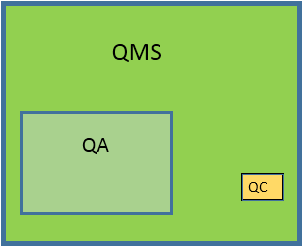
Difference between Quality Control and Quality Assurance:
Quality Control (QC) | Quality Assurance (QA) |
---|---|
Focus on the detection of defects | Focus on the prevention of defects |
Responsibility for a specific team | Responsibility for all team |
It is a reactive activity | It is a proactive activity |
It is related to the product | It is related to the process |
It is done at the final e.g Final Inspection | It is done from development to the final process |
Fix it whenever it goes wrong | Do it the right first time |
It includes inspection as per the specification | It includes quality audits, Quality Procedures, training etc |
Increase cost, rejection etc | Overall less cost & less rejection |
There are chances of defect skip | It provides confidence in the quality |