Kanban is a workflow management method focused on continuous improvement. It operates as a pull-based system, meaning tasks are pulled through each stage only when capacity is available, rather than being pushed through regardless of readiness.
While commonly used in production, Kanban is adaptable to a wide range of processes. Its core purpose is to help teams visualize their work, limit work in progress, and identify bottlenecks. By making the flow of tasks more transparent, Kanban enables teams to pinpoint issues and take informed steps to optimize their processes.
Kanban is a method used to manage and improve workflows. It was first developed for manufacturing but is now used in many industries like software, healthcare, and retail. Kanban supports inventory control in Just-in-Time (JIT) manufacturing. It was created by Taiichi Ohno, a Japanese engineer at Toyota. The word “Kanban” means “visual cards” in Japanese.
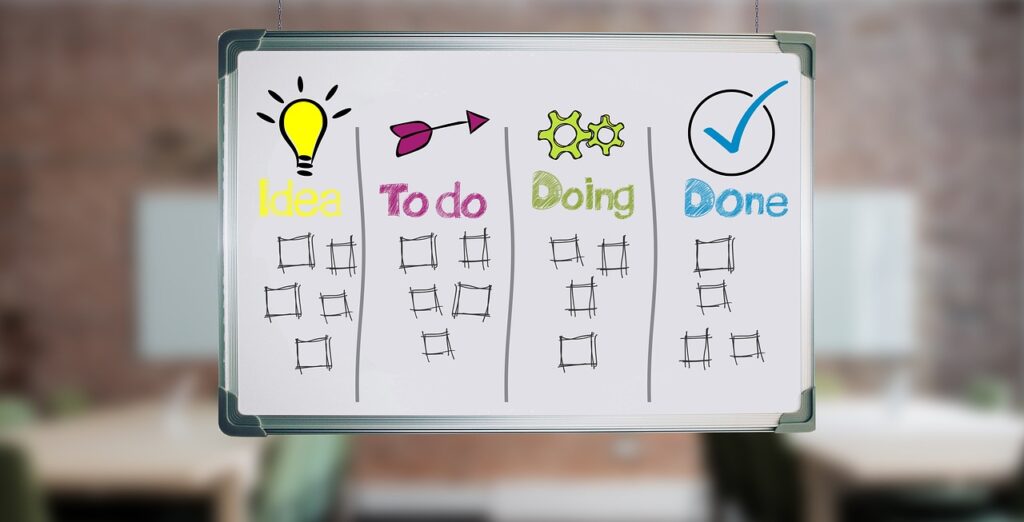
Benefits of the Kanban System:
Some benefits of a Kanban system are as below:
Kanban board provides a clear visual representation of the work being done. Who is working on it and the current status of each task? This helps team members stay informed.
Kanban is a pull-based system, which means that tasks are only pulled into the workflow when resources are available. This allows teams to adapt to changing priorities and unexpected interruptions.
By limiting work in progress and focusing on one task at a time, kanban can help teams complete tasks faster.
Kanban encourages teams to regularly review and optimize their workflow, leading to ongoing improvements in efficiency and productivity.
Kanban’s visual system makes it easy for teams to collaborate and communicate on projects, improving overall team performance.
What are the four principles of Kanban?
The Kanban Method, developed by Taiichi Ohno for Toyota in the 1940s, has four core principles:
- This involves creating a visual representation of the work process and the flow of materials or goods through it. This can be done using a Kanban board, which shows the status of work items at different stages of the process.
- By limiting the number of work items that can be in progress at any given time. Teams can reduce multitasking and increase focus on completing work items. This helps to prevent bottlenecks and improve flow.
- By closely monitoring the flow of work through the process, teams can identify and address bottlenecks and other issues that may be impacting productivity.
- Making the rules and policies governing teams can ensure that everyone understands how the process is supposed to work. Also it can work together more effectively.
These principles work together to create a pull-based system, where work is pulled through the process in response to demand, rather than being pushed through based on a schedule or forecast. This helps to improve flow, reduce lead times, and increase overall efficiency.
What is a Kanban Board?
A Kanban board is a visual management tool used to help teams manage and organize their work. It is typically used in the context of agile software development but can be applied to any workflow. The board typically includes columns that represent different stages of the workflow, such as “To Do,” “In Progress,” and “Done.” Cards, representing tasks or work items, are placed in the appropriate column as they move through the workflow. The goal of the Kanban board is to help teams visualize their work and identify bottlenecks or areas for improvement in their process.
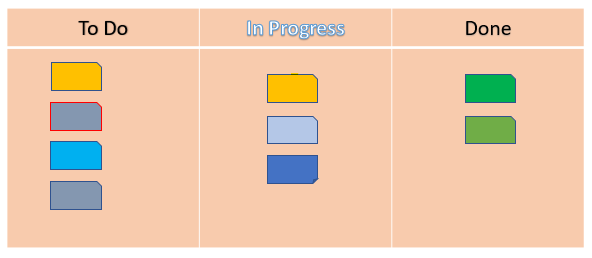
Example of Kanban:
An example of a Kanban board for a software development team might include columns for “Backlog,” “To Do,” “In Progress,” “Code Review,” and “Done.” The “Backlog” column would contain items that have been identified as work that needs to be done but have not yet been prioritized. The “To Do” column would contain items that are ready to be worked on. As a developer begins work on a task, they would move the corresponding card from “To Do” to “In Progress.” Once the task is complete, it will move to the “Code Review” column for review by other team members. Once the code has been reviewed and approved, it will be moved to the “Done” column.
Kanban boards are flexible and can be adapted to suit the needs of different teams and organizations. For example, a retail company could use a Kanban board to manage its inventory, with columns for “Incoming,” “On Hand,” “On Order,” and “Sold.”
Kanban boards are a visual representation of the work being done; they can help team members understand what work is currently being done, and what is upcoming and also help in identifying bottlenecks or areas for improvement in the process.
You may like to read about other lean tools: Jidoka, Poka Yoke
Kanban system in production:
In production, a Kanban system is used to manage the flow of materials and goods through the production process. It is a pull-based system, meaning that production is driven by demand from downstream processes or customers, rather than by a schedule or forecast.
A Kanban system in production typically includes the following elements:
- Kanban cards: These are used to signal the need for more materials or goods and to authorize the release of materials or goods from a preceding process.
- Kanban boards: These are used to visualize the flow of materials or goods through the production process.
- Kanban loops: These are used to link different processes together and to coordinate the flow of materials or goods between them.
An example of a Kanban system in production might include a manufacturing facility that produces car parts. The facility might have a series of processes that include stamping, welding, painting, and assembly. Each process would have its own Kanban board to visualize the flow of parts through that process.
Kanban cards would be used to signal the need for more parts from upstream processes and to authorize the release of parts from downstream processes. This way the facility can ensure that it has the right parts at the right time to keep the assembly line moving.
The Kanban system in production helps in maintaining inventory levels, reducing overproduction, improving the lead time and increasing the overall efficiency of the production process.