Poka-Yoke:
Poka Yoke means Mistake Proofing or Error Proofing. Poka Yoke is a mechanism to prevent mistakes and defects from being made or detect mistakes if not prevented. It is also called error-proofing or foolproofing.
Dr. Shigeo Shingo developed the concept of Poka-Yoke. Poka-Yoke is based on the concept that people do not make mistakes intentionally. But for other various reasons, mistakes can happen. Also as per Toyota’s concept, an error is the failure of the system & methods that are used to perform that work.
But in general, operators are blamed for any mistake. So there is a need for Poka-Yoke or mistake-proofing to be implemented in all methods or systems.
Shingo Statement about Errors & Defect relationship:
“The causes of defects lie in operator errors and defects are the result of neglecting those errors. It follows that mistakes will not turn into defects if operator errors are discovered and eliminated beforehand.
Defects arise because errors are made; the two have a cause-and-effect relationship. Yet error will not turn into defect if feedback & action take place at the error stage.“
Poka-Yoke works as Zero Defect:
When we implement poka yoke in the process (tools/machine) to prevent defects from occurring. Then we got a condition of zero defects. So poka-yoke works as a zero defect in any process or system. Also defect prevention is the goal of IATF 16949. So we should focus on error-proofing from new development to mass production.
Dr. Shingo identified 3 types of inspections:
100% Inspection:
This involves sorting the defects out of the acceptable products. Shingo said that inspection of quality is not an effective quality management approach. As it is a very costly process to inspect 100% parts. After that also there are also chances of human error. So we never prevent defects from passing by 100% inspection/segregation.
Sampling Inspection:
This uses data gained from inspection to control the process & prevent defects. SPC is a type of sampling inspection. But as per Shingo’s concern, inspection may not occur soon enough after production. So there are chances to skip defects. So there are chances of rejection to be made in the meantime of the inspection frequency decided.
Source Inspection:
Operators check their work while doing production. This gives current & real feedback. Self-check uses poka-yoke devices to allow operators to assess the quality of their work. Because they check each part produced, operators may be able to recognize what conditions changed that caused the last unit to be defective. This concept is used to prevent further defects.
In source inspection, poka-yoke devices ensure that proper operating conditions are available before actual production. The poka-yoke devices & inspection techniques are intended to increase the speed with which quality feedback is received.
Mistake-proof design :
It is a method to avoid mistakes by designing items so that they can only be assembled (Design for Assembly, DFA) in a certain way. So it is called mistake-proof design because it does not take much skill to put the parts together.
Examples of foolproof design in daily use:
- Mobile phone SIM card: In a mobile SIM, there is a cut in one corner, so it can fit in the mobile SIM cavity only in a fixed direction & location. There is no chance of the SIM fitting in the wrong orientation.
- Pen drive in USB: Same is the case with a USB pen drive, which can fit only in one direction.
- Three-pin plug: Due to the design of the 3-pin plug, there is no chance for the plug to be fitted in the wrong direction.
- Two Pin Plug: As the figure below shows, there is no chance of wrong fitment.
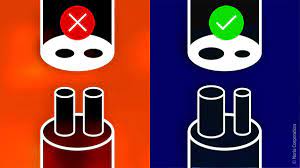
Awareness about Poke Yoke :
To make poka-yoke a company-wide program, first, you need to educate your operators on the concept of mistake-proofing. Also, you need to empower them to make small improvements in their processes continuously (Kaizen).
Then we will get an industry wasting less energy, time & resources in doing things wrong and then reduce the cost of poor quality ( COPQ).
You may like:
Overall Equipment Effectiveness (OEE)
Kobetsu Kaizen in manufacturing (TPM)
Thank you a lot for sharing this with all people you actually understand what you’re speaking approximately!
Mate, this website is definitely fabolous, i merely love it
self publishing is kind of difficult at first, but you can easily learn the tricks of the trade ,,
very good post, i definitely adore this site, persist in it