Purpose of APQP :
To define the procedure for APQP (Advanced Product Quality Planning) activities including various stages of development of Prototype/Product sample, Pre-launch, Production and mass production. To facilitate communication with all concerned within the organization and also with suppliers and customers, to ensure that all required steps are completed on time.
- Purpose of APQP :
- Scope of APQP:
- Responsibility for APQP:
- Process of APQP:
- APQP PHASES :
- Engineering Change Note (ECN):
- APQP Phase-wise documents as per AIAG Requirements:
- APQP phases and activities PDF:
- APQP-related requirements as per the MACE VSA check sheet:
- Clause 1: Production Preparation/New Product Development
- 1. Regarding the implementation rule of production preparation
- 1.2 Regarding management/implementation by production preparation plan/report (master plan)
- 1.3 Defect prevention on the stage of process design by using FMEA/Matrix diagram
- 1.4. Product/process evaluation at the quality evaluation meeting in each trial
- Clause 1: Production Preparation/New Product Development
Scope of APQP:
This applies to the following products if there is:
AA – New component: No experience in production so far
A – Similar parts that have been produced earlier
B – Part happens to be a major deviation in the component, ECN, PCN, i.e. Part profile change, the process added, a new tool developed, major rectification in tools.
C – Part happens to be a minor deviation in the component i.e. Minor rectification in the tool, process sequence change, process layout change.
D– Plant Location Change.
E– Supplier Change
F– Raw Material Change
Responsibility for APQP:
The overall responsibility for the implementation of this procedure lies with the Team Leader (Design and development Head) with the support of all functional heads.
Process of APQP:
The five phases of Quality Planning are considered the basis for the process of planning. The organization falls under the category of `Manufacturing only’ as per the customer requirement of Advanced Product Quality Planning.
APQP PHASES :
1. PLAN AND DEFINE :
- Receipt of the Part drawing, along with the specification drawing /reference sample. A cross-functional Team for every project is organized by the concerned Development agency and the Project Leader shall be nominated by the Team Members for coordination of the project activities.
- CFT Formation:
- Select a Project Team Leader responsible for coordinating the project activities.
- Define the role and responsibility of each member represented on the APQP Responsibility Matrix.
- Feasibility Study:
- The Risk Assessment Sheet is filled and the feasibility study records and assesses the manufacturing feasibility covering new process design or assessment of existing processes. Identify costs, lead time, and constraints that must be considered. Determine the assistance required from the Customer & confirmation from the customer.
- Send a quotation to the customer based on the costing sheet after approval.
- Receipt of LOI/PO from customer & approval of the same from MD. (Letter of intent/Purchase order)
- Follow the APQP matrix & preparation of the APQP Timing Chart ( Development Plan) as per the APQP matrix.
- Preparation of Preliminary Process Flow Diagram.
- Past defect history study & lesson learning. (Past Trouble Data Sheet)
- Preparation of Bill of Material & develop/select a supplier.
Review Mechanism- The timing plan shall be reviewed by the team leader with CFT every week and Top Management shall review every month to check the effectiveness of planned activities and prepare MOM for each review.
Note: Review frequency can be changed as per the project duration.
2. PRODUCT DESIGN AND DEVELOPMENT:
- Identify new equipment and facility requirements.
- Identify new tools, instruments, gauges, and fixture requirements.
- Regulatory requirements identification.
Note: If a company is manufacturing only (Design provided by the customer), then there is no need for these phase activities.
3. PROCESS DESIGN AND DEVELOPMENT:
Based on the inputs from the customer and a feasibility study, the concerned development team shall carry out risk assessments. In sample development, the Development department shall perform the following major activities.
- Identify or list Special Characteristics and participation in Specification meetings at the customer end and keep evidence of the meeting if taking part in spec. review meetings.
Special Characteristics:
- Special characteristics are those characteristics that require statistical process control (SPC). Special characteristics and critical dimensions will be considered as per the criteria below:
- Special characteristics should be defined based on Fit, Function, Formation, Safety, Appearance, and Legal. ( FFFSAL). Special characteristics shall be cascaded in all process documents like Drawing, FMEA, Control Plan, and Operation standards.
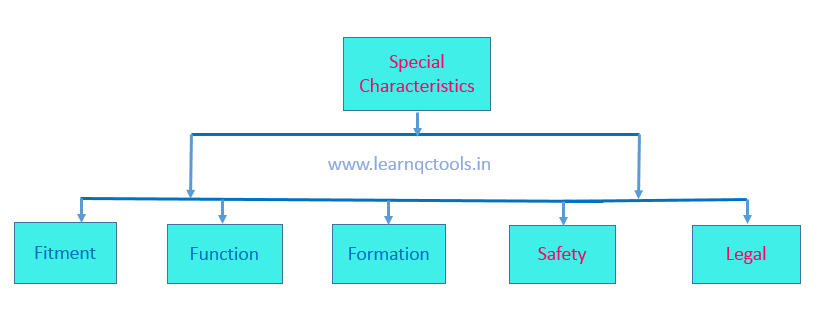
- Preparation of process FMEA
- Preparation of Proto/ Prelaunch control plan.
- Tool development plan or tool receipt from the customer
- Procurement of new machines, equipment, tooling, fixtures, gauges, and raw materials.
- Provide training to the concerned person.
- Producing T0 Samples & submitting them to customers with the inspection report.
- Get approval from customers & feedback.
- Implement correction if required.
- Producing T1 sample
- T1 sample submission along with the inspection report.
- Get approval from the Customer & feedback
- Implement correction if required
In case samples are not approved by the customer, continue to submit samples till approval after corrections.
The design and development head shall also prepare the Tool Development Plan for a sample of the new product when making the Process Flow Diagram. The tooling, which is offloaded, has to be followed and tracked with the supplier for their progress and timely execution.
The records shall be generated and maintained as per Customer Specific Requirements (CSR)
The design & development head shall generate monthly information reporting the status of sample development, including the status of approval of the customer for management review.
Sample development orders are closed after receiving an acceptance report from the customer. In case the samples are not accepted, the Development Engineer shall study the feedback report and coordinate with other relevant departments and review APQP activities & restart exercises.
4. PRODUCT AND PROCESS VALIDATION :
- Carry out the Pilot lot production as per the Control Plan by using Production Tooling, Inspection Gauges and instruments. Prepare pilot lots ( Prepare min 100 parts )
- Conduct tests if any are required
- Prepare & finalize process documents:
After the customer approval, update the following process documents if any correction is required.
List of Process documents:
- PFMEA review changes if any
- Control Plan
- Operation Standard
- Work Instruction
- Process flow diagram
- Packing Standard: Finalize a suitable packing standard
After pilot lots, Initial supply control shall start from the in-house SOP up to three months after SOP starts at the customer end. Parts will be monitored under initial supply or initial production control as per the Initial Supply Control procedure.
- Handover to Production-
All required activities, resources like JIG/ Fixture / Tool / Manpower / Working Table / Lighting / Inspection aid/Operation Standard/Control Plan /PFD/PFMEA/WI handover to production in the Data Handover Checklist and Production Team to be ensured before starting of production for New Part / Change parts.
If the samples are not accepted, the Design and Development head will study the feedback report, coordinate with other relevant departments, and review APQP activities & restart exercises.
5. FEEDBACK, ASSESSMENT AND CORRECTIVE ACTION:
Take feedback from the customer end till SOP at the customer end. CFT identifies the causes and initiates corrective actions in the PDCA sheet, wherever required, to improve the reduction in variation and enhance customer satisfaction.
Engineering Change Note (ECN):
When ECN is received from the customer end for a minor change in a newly developed component / Existing supplied component or extremely minor change in details related to the component.
- The design and development head checks the feasibility as per design requirements.
- Engineering change note request raised to the concerned department.
- After doing the needful correction as per ECN, Validate the Process and product.
- Prepare the samples & generate the ECN report & submit a sample to the customer as per APQP Matrix for getting approval & feedback.
- In case, if the customer requires any correction in samples then resubmit the sample after the required rectification till customer approval.
- After that use the identification tag in 3 lots for ECN part supply.
- If any ECN is raised internally for any product level change, approval from the customer must be taken.
Disposal Criteria of Pre-ECN Parts :
Before ECN parts are dispatched to the customer, confirmation is required from the Customer.
T0 & T1 parts are to be kept in the Lock & Key trolley/bin, keep only updated parts, scrap the unapproved parts and keep the record in a scrap note.
APQP Phase-wise documents as per AIAG Requirements:
Phase 1: Plan and Define:
- Cross-Functional Team
- Feasibility Study and Risk Analysis
- Preliminary Process Flow Diagram
- APQP Timing Plan
- Past Defect history and lesson learning sheet (Past Trouble Data Sheet)
- Bill of Materials
- Special Product and Process Characteristics
Phase 2: Product design and development:
- Identification of new equipment and facilities
- Identification of new Tools, Instruments, gauges, and fixture requirements
- Statutory and regulatory requirement identification
Phase 3: Process design and development:
- Process Flow Diagram (PFD)
- Process Failure Mode and Effect Analysis (PFMEA)
- Prelaunch Control Plan
- Inspection standards (Incoming, In-process and Final)
- Tools, Fixtures and Gauge Development Plan
- Inspection and validation of tools, fixtures and gauges
- Training record to the concerned person
- Inspection report of T0, T1 samples
- Customer Approval report of T0, T1 samples
Phase 4 Product and Process Validation:
- Product and process audit report
- MSA report
- SPC report
- Finalize process documents
- Packing Standard
- PPAP documents
- APQP sign-off sheet
Phase 5 Feedback Assessment and Corrective Action:
- Customer and in-house feedback analysis and corrective action (PDCA Sheet)
- Handover to the production department.
APQP phases and activities PDF:
APQP-related requirements as per the MACE VSA check sheet:
Clause 1: Production Preparation/New Product Development
1. Regarding the implementation rule of production preparation
1.1 Do you define the procedure for Product development including the following? -scope of parts, responsibility of each department, control contents/items?
- Procedure for product development from receipt of order to SOP at customer end (preferably as per AIAG guidelines) to be available
- APQP matrix for deciding development activities based on the categorization of parts (for new and modifications). Roles and Responsibilities are defined in the APQP matrix. Activities matching with the procedure (minimum NPD, ECN, PCN, Plant location change, Supplier change, RM Change to be addressed in the matrix, critical activities e.g. Tool development, supplier development etc, to be identified)
- Understanding of Team
1.2 Regarding management/implementation by production preparation plan/report (master plan)
1.2.1 Do you implement follow-up to control the schedule and progress of production preparation items? Incl top management
- Customer events (sample approval, trial dates, SOP at customer end) and vendor events (sample submission, pilot lot submission, SOP) are to be mentioned in the timing plan.
- Activities matching the procedure and APQP matrix
- Evidence of review by the project leader and top management in the timing plan
- MOM or record of reviews (for evidence)
- Micro timing plan matching with MACRO plan (wrt timing)
- Capturing delays in plan v/s actual in timing plans
- RFQ register (status of the inquiries to be checked)
- The timing plan approved by top management
- Evidence of activities
1.3 Defect prevention on the stage of process design by using FMEA/Matrix diagram
1.3.1 Do you consider the following items and implement corrective and preventive action to the processes and standards before regular production? –Troubles in the past; -Defect items expected; -Defect items unable to capture at the customer; -Defect items difficult to repair.
- Procedure for FMEA with CFT approach
- List of problems reported in the past at the customer end, in-house, development and supplier (Things gone Wrong) (lessons learned from experience/kakotora sheet)
- Rating of FMEA as per AIAG guidelines and having backup data for rating. Allocation of severity, occurrence & detection as per the AIAG manual
- Cut-off criteria for taking action as per the latest AIAG manual
- Review plan for FMEA and evidence of review as per decided criteria and at decided frequency.
- Evidence of implementation (FMEA)
1.4. Product/process evaluation at the quality evaluation meeting in each trial
1.4.1 Do you prevent defects by quality-improving activities of cross-functional teams to evaluate quality performance?
- Summary in the PDCA sheet
- Summary of Adequacy of Analysis
- Effectiveness of countermeasures
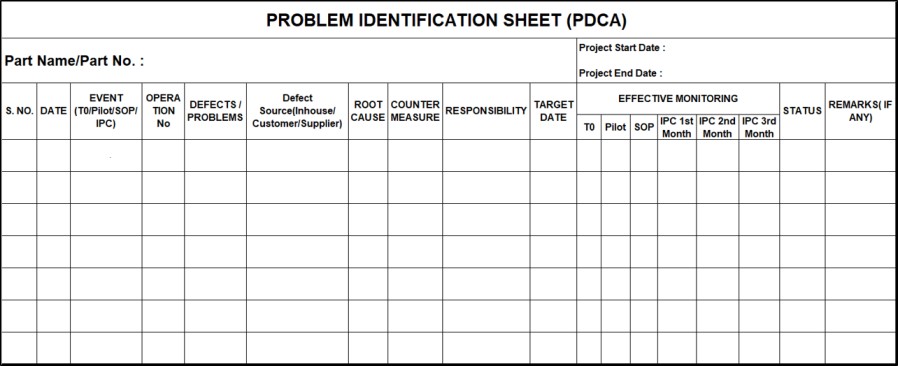
Read more about:
Initial Production Control Procedure / Initial Flow Control / Initial Supply Control
Very nice blog! Thanks for sharing.
Thanks Gunjan for your feedback
Thanks you so much for such easy explanation….
Thanks for your valuable feedback.
Dear sir ,
Kindy share the handling of customer properties procedure
https://learnqctools.in/handling-customer-property
Dear team ,
kindly share the escalation process/ procedure at shop floor if found any Non conformity
Greetings of the day
kindly share the Dock Audit & Layer process Audit & Product Audit check points details which helps to strengthen further more audit points.
Dear sir ,
Greetings of the day….!!!
i would like say my thanks to you for shared the details of my earlier request.
Now i am leave a new request to you for new information request in welding process.
kindly share the MIG & Projection &Spot welding process validation report format/procedure for both manual & Robot Welding , also share what are the things need to consider during welding process validation .
Thanks
Share Process design plan, input, review, output records formats who are not responsible for product design.
Very well made. In this procedure, esp. APQP Phase-wise documents, are they updated as per APQP March ’24 latest edition?