Purpose of FMEA:
The purpose of FMEA is to establish & maintain a procedure for process failure.
Scope of FMEA:
This procedure applies to all processes (major & critical) that are being used to make various products.
- Purpose of FMEA:
- Scope of FMEA:
- What is an FMEA process?
- Who is responsible for conducting FMEA?
- Procedure for FMEA:
- Input for FMEA:
- FMEA revision rule:
- Severity :
- Occurrence:
- Detection:
- Risk Priority Number (RPN):
- FMEA Example :
- FMEA cut-off criteria :
- PFMEA review criteria:
- Severity Ranking Chart:
- Occurrence Ranking Chart :
- Detection Ranking Chart:
- Occurrence Rating Sheet :
What is an FMEA process?
An FMEA process can be described as a synchronized group of activities intended to recognize and evaluate a product/process’s potential failure and its effects.
- Identify actions that could determine or reduce the chance of the potential failure occurring.
- To document the process.
Who is responsible for conducting FMEA?
Head development is responsible for conducting FMEA with the help of various section heads who are in charge of different processes like QA, Production, Tool Room, Purchase, Engineering etc
Procedure for FMEA:
Head development creates the process flow chart and identifies critical/ special processes. FMEA teams are divided into departments, which include Head Development, Head QA, Head Production, and Head Material. These departments are assigned the responsibility for conducting FMEAs.
FMEA teams look at the following factors.
a) Identify potential product-related process failure modes.
b) Assesses the potential customer effect of the failure.
c) Identify the potential manufacturing or assembly process causes reduction and identify the process variable on which to focus control for the occurrence, detection of the failure conditions.
d) Develop a ranked list of potential failure modes, thus establishing a priority system for corrective action consideration.
Input for FMEA:
The following points are to be considered while making PFMEA:
- Past defect history and lesson learning ( Customer + Development Stage + In-house Problems included)
- Occurrence calculation sheet.
- Defect item expected
- Process Flow Diagram (PFD)
- Part Drawing
- Similar Part Control Plan & FMEA.
- Occurrence Rating Chart
- Detection Rating Chart
- Severity Ranking Chart
FMEA revision rule:
- FMEA is to be reviewed at the time of market failure.
- When Customer complaints are received
- When any critical issue/rejection occurs in-house.
- FMEA is also revised annually to consider product requirement & potential failure & their effects.
- When horizontal deployment is in a similar part or process.
The various FMEAs are filled in the same manner as referred to in the marking manual for FMEA. FMEA assesses through their experience & available data by the following factors:
Severity :
Severity is an assessment of the effect of the potential failure mode on the customer. Severity applies to the effect only. The severity should be estimated on a 1 to 10 scale. The rating is done strictly as per the chart for severity ranking.
Occurrence:
Occurrence is how frequently the specific failure cause/mechanism is projected to occur. The occurrence ranking number has meaning rather than a value. Occurrence ranking numbers are also given as per the FMEA manual using the evaluation criteria chart. Estimate the likelihood of occurrence on a 1 to 10 scale. Only occurrences resulting in the failure mode should be considered for this ranking.
Detection:
Detection is assessed by the team based on the probability that the current process control will detect or not. The potential cause/mechanism or the probability that the proposed process control will detect the subsequent failure mode before the part/component used in manufacturing/process locations. Detection ranking is given based on the suggested evaluation criteria given in the FMEA chart on a 1 to 10 scale.
Random quality checks are unlikely to detect the existence of an isolated defect and should not influence the detection ranking. Sampling done on a statistical basis is a valid detection control. Do not automatically presume that the detection ranking is low because the occurrence is low, but do assess the ability of the process control to detect low-frequency failure modes or prevent them from going further in the process.
Risk Priority Number (RPN):
The risk priority number is the product of Severity (S), Occurrence (O), and Detection (D) ranking.
RPN = Severity x Occurrence x Detection = S x O x D
This value should be used to rank the concerns in the process. The RPN will be between 1 and 1000. For higher RPN the team must undertake efforts to reduce this calculated risk through corrective actions. Regardless of the resultant RPN, special attention should be given when the severity is high.
Note: RPN is eliminated as per the latest AIAG VDA FMEA.
FMEA Example :
Here is an example of the process FMEA of the combined Parting, drilling and chamfering process in CNC machining.
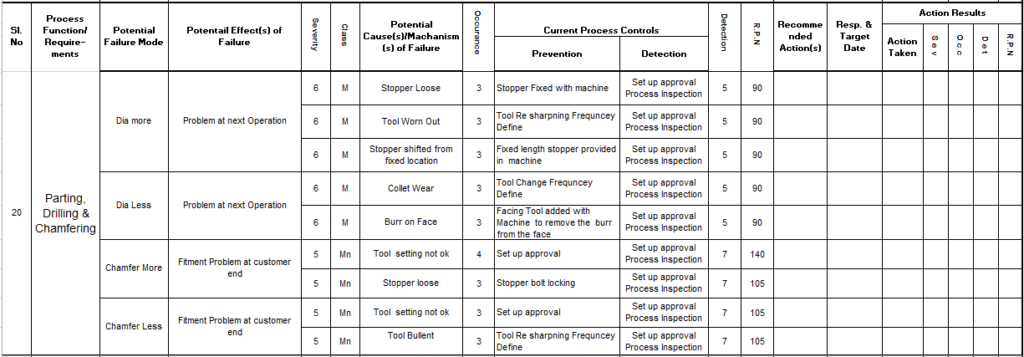
In this machining process, there are 4 failure modes identified. These failure modes are Dia more, Dia less, Chamfer more and Chamfer less. But failure mode ‘chamfer more’ due to the tool setting not OK has the highest RPN of 140. So, there is a need to take action first on the cause of failure.
FMEA cut-off criteria :
Check the rating of severity, occurrence & detection.
- If it is more than 8, then take action first on that.
- If all are less than 8, then focus on the top 1 RPN.
PFMEA review criteria:
Review PFMEA in the following conditions:
- Customer complaint (immediately to be updated)
- Major In-house defect ( immediately to be updated)
- Market failure (immediately to be updated)
- Once a Year
- Horizontal Application
- Any ECN / PCN or other changes
Severity Ranking Chart:
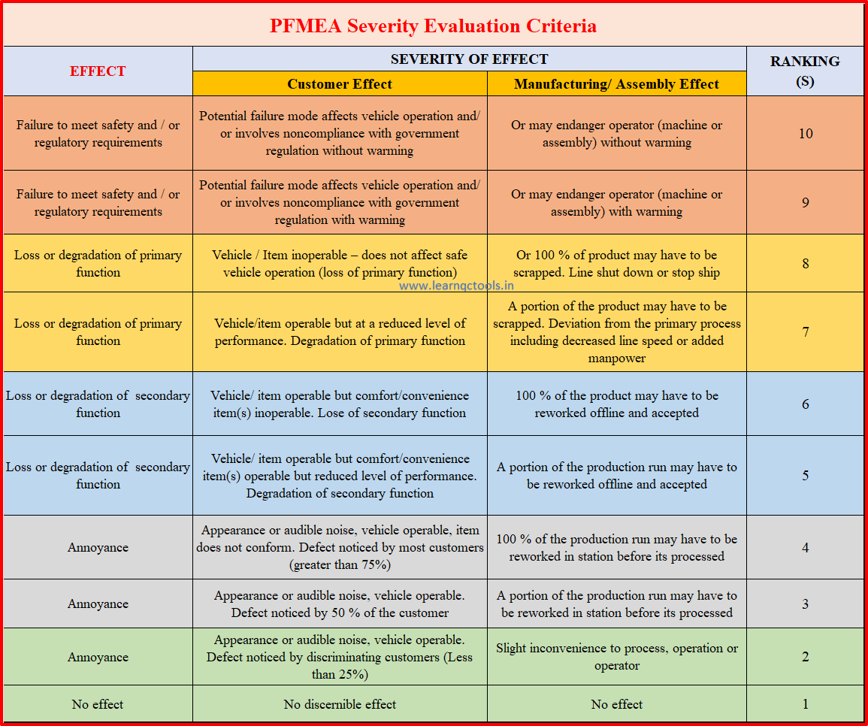
Occurrence Ranking Chart :
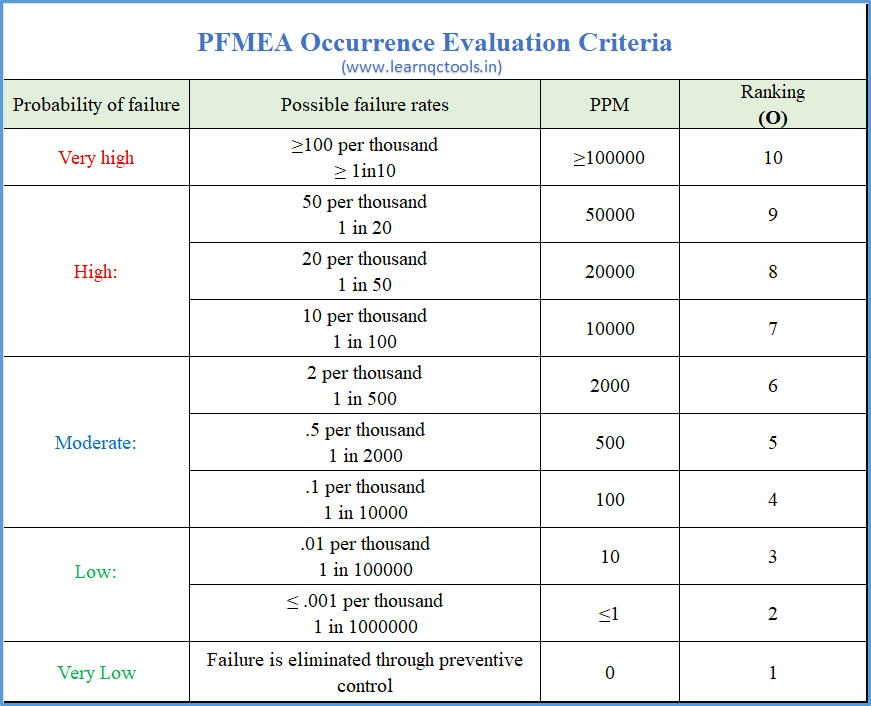
Detection Ranking Chart:
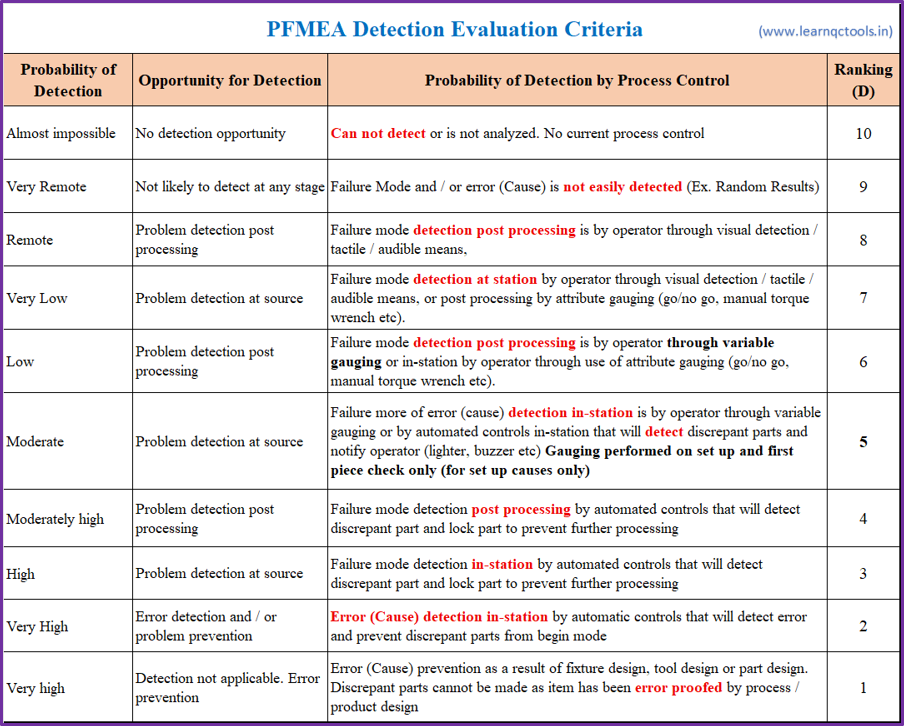
Occurrence Rating Sheet :
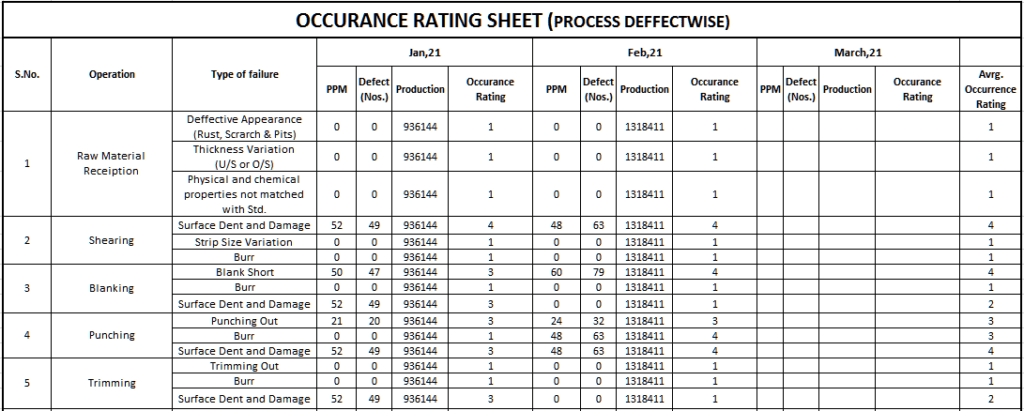
You may like to read about AIAG VDA FMEA, AP Tables & New Format