Purpose:
To understand clearly abnormality and abnormal situations, to make operators understand abnormality and abnormal situations, and to standardize further the rules and routes to handle such situations. To learn about handling abnormality in quality.
Scope:
Handling in-process complaints, supplier complaints & customer complaints and abnormal situations.
Abnormal situation:
An abnormal situation occurs when a process variable goes outside its operating range and may become an emergency if not controlled by an appropriate response/action.
An abnormal situation in manufacturing refers to an unexpected event or deviation from normal operating conditions that can lead to reduced productivity, increased costs, or even safety hazards.
Examples of abnormal situations in manufacturing include equipment failures, power failures, natural disasters, human errors, and changes in demand or supply. These situations can cause disruptions in the production process and require a quick and effective response to minimize their impact on manufacturing operations.
Responsibility:
S.No | Activity | Responsibility | Frequency |
---|---|---|---|
1 | List of Abnormal Situation and their Reaction Plan | Production Head/ Shift In-Charge | Need-based |
2 | Handling complaints from customers | Quality In-charge | Need-based |
3 | Handling in-process complaint | Quality In-charge | Need-based |
4 | Handling the abnormality of the supplier | Quality In-charge | Need-based |
Procedure :
Abnormal Situation Handling:
Abnormal situations are defined and display process-wise in Shop floors (Press Shop, Weld Shop, Machine Shop etc) as per work instructions.
The production supervisor informs the concerned person & after that identifies the root cause & analysis is done about the issue/situation. After that Production supervisor/ Quality Engineer shall record the abnormal situation in the 4 M Change tracking sheet.
The operator/concerned person identifies the abnormal situation, stops production & immediately informs the production supervisor for further action.
List of abnormal situations in the manufacturing industry:
Abnormal situation examples:
- A machine is producing defective parts continuously.
- Repeated breakage of production equipment (m/c, tool & fixture).
- The operator produces defective parts continuously.
- The operator detects defects produced by the previous process.
- Poka Yoke does not detect defective parts ( Poka Yoke not working)
- The inspector fails the Poison test
- Poke yoke bypassed
- Absenteeism is more than the Attrition rate
- Parts fallen down
- Bin fell down
- The instrument has fallen down
- Instrument showing error
- Gauge fallen down
- Power Failure (Projection/Spot)
- Machine parameters found out of spec during routine checking
- Different grade materials are used
- The production runs on a lower-tonnage machine.
- The production runs on temporary Fixtures/tools/dies.
- The operator of under skill deputed
- Overtime (Working more than 12 hours)
- A machine is producing abnormal noise.
- The machine takes the stroke without pushing the paddle.
- The instruments found out of calibration.
Abnormal situation work instruction:
Customer Complaint Handling:
- As soon as the customer raises the complaint (by email/telephone), record it in the customer complaint register. Inform the concerned persons, including top management.
- Check all available stock (FG, WIP and Customer-end) for the raised complaint.
- Make the operators aware of the In-house/Customer complaint. Display a one-point lesson (Quality alert note) to aware the operators and final inspectors.
- Analyze the root cause of the problem with the cross-functional team (CFT), take required countermeasures, and submit an action plan within one week in a customer-required format. (DAR/CAPA format or customer-approved format) or as per customer requirement.
- Standardize the related documents like FMEA, Control Plan, Operation standard & WI etc against the countermeasure.
- Check the effectiveness of countermeasures taken for up to three months.
- Check the feasibility of horizontal deployment of countermeasures in similar parts/processes after verification of countermeasure effectiveness.
- In case the problem repeats then again why-why analysis done for the same defect.
How to solve the complaints with the 8D problem-solving methodology.
Handling in-process complaints:
Put a Red bin near each machine to store non-conforming parts. The QC Inspector shall identify a part defect during a patrol inspection. Then Non-Conforming part is moved to the Red Bin and Red Bin Analysis is done daily in the Red Bin Analysis record.
Suspected Parts Handling:
Put a yellow bin at the PDI & Shop floor area to store Suspected Parts that fall during production/part movement/part inspection. QC and production supervisor jointly check/inspect these suspected parts and the action taken is mentioned below:
Types of Part | Action |
---|---|
OK Parts | Send for PDI |
NG Parts | Send for Red Bin |
WIP Parts | Handover to Production |
- Make a summary of all the defects that occurred at the end of the month.
- Make a Pareto chart of defects and parts and take action on the top defects. Select all the department’s top defects for analysis. e.g. Machine shop, Press shop, Weld shop, Assembly shop etc.
- Check all available stock (FG & WIP) as per the lot no. & batch number for the raised complaint if required. Also inform the customer in case of outflow to the customer.
- Make the operators aware of the complaint. Display a one-point lesson (Quality alert note).
- Analyze the root cause of the complaint with a cross-functional team (CFT) and take required countermeasures.
- Standardize the related documents like FMEA, Control Plan, Operation Standard & WI etc against the countermeasure.
- Check the effectiveness of countermeasures for up to three months.
- Check the feasibility of horizontal deployment of countermeasures in similar parts/processes after effectiveness OK.
QPCR raising (DAR) Criteria :
In-house QPCR will be raised by QA under the following conditions:
- The top one defect as per the Pareto chart monthly before the 10th of next month
- Assignable cause (Rejection of more than 10 pcs) in a day of any part.
- For any critical defect.
Defect Analysis Report (DAR) format:
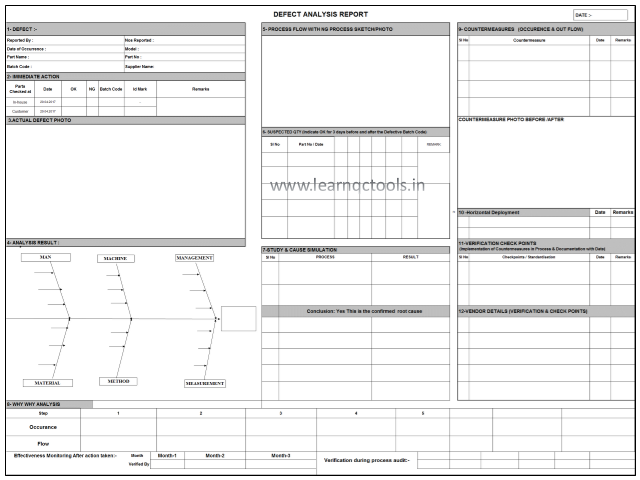
Supplier complaint handling:
- QPCR is to be raised to the supplier for receipt rejection, for line-reported and customer-reported defects ( for dimensional & fit function ) and recorded into the Supplier complaint register.
- Check all available stock (FG, WIP and Raw Materials) for the raised complaint.
- Make the operators aware of the complaint. Display a one-point lesson (Quality alert note), if possible, within the period.
- Analyze the root cause of the complaint with a cross-functional team (CFT) and take required countermeasures.
- Standardize the related document against the countermeasure.
- Check the effectiveness of countermeasures for up to three months.
- Check the feasibility of horizontal deployment of countermeasures in similar parts/processes.
Checkpoints as per Maruti Center for Excellence (MACE) VSA sheet:
Handling an abnormal situation
Do you clearly define what an abnormal situation and make operators know the definition?
Sub Question |
---|
What is the definition of abnormal situations? |
Are the abnormal situations displayed on the shop floor? |
Check the awareness of abnormal situations among the shop floor personnel |
Do you clarify and standardize the handling rules/routes for customer claims, in-process failure and supplier failure?
Sub Question |
---|
Check the availability of Procedures for handling customer complaints, in-process failures and supplier defects |
Criteria for raising QPCR (internal QPCR to be raised in case of daily abnormal rejection and monthly top rejections) |
Check for the availability of the customer complaint register and QPCR control registers (for in-house and supplier defects) |
Do you have criteria to estimate the scope of the suspected lot for abnormal situations? When an abnormal situation occurs, do you trace the suspected lot based on the criteria?
Sub Question |
---|
Check the criteria to estimate the suspected quantity produced during abnormal situations and the system to trace suspected lots produced based on the criteria. |
Check the record of parts produced during abnormal situations |
Check for their Traceability |
Prevention of recurrence. -Customer claims -In-process failure -Suppliers failure
Do you prevent the recurrence of issues by analyzing the cause of occurring defects based on process investigation results such as 5-why analysis?
Sub Question |
---|
Analysis sheet ( A3/CAPA) for analyzing customer complaints, in-house defects and supplier defects |
Monthly in-house rejection analysis (defect-wise Pareto and analysis) |
Quality of analysis (root cause analysis) |
Non-conforming parts produced due to defects (Reported at the customer end, inhouse defects or supplier defects) checked or not |
Do you reflect corrective action to improve process control and review of standards?
Sub Question |
---|
Check the Countermeasures detail for the root cause |
Standardization (Control Plan, WI/OS Inspection standard, check sheets, list of abnormal situations etc.) |
Check for the updation of PFMEA |
After corrective actions are taken, do you conduct an on-site check and evaluate the effectiveness? And horizontal deployment.
Sub Question |
---|
Evidence of onsite verification of countermeasures (to be checked for min three months) |
Check for Horizontal deployment of countermeasures |
Effectiveness of countermeasure (to be checked for min three months) |