Purpose:
Coherence between all the documents, such as the Customer Inspection Standard of parts with the Control Plan, Operation Standard, Inspection Standard, and packing Standard, is essential. Properly defining the standards can prevent rejection and rework and thus improve OEE and COPQ.
Responsibility :
S.No | Activity | Responsibility | Frequency |
---|---|---|---|
1 | Review of the Standards/ Format/ WI/ Procedures etc. | Quality Incharge / MR | In the event of a change, Once in a year, Customer-specific requirement, Customer complaint |
2 | Updating of standards | Quality Incharge/MR | After every change |
3 | Issue of the revised standard | Quality Incharge/MR | After every change |
Procedure:
CASE-I Procedure for Standard Management:
- Are the Control Plan, Operation Standard and Inspection Standard available for all the parts? If not discuss with the concerned department and ensure availability for all the parts.
- If unavailable, draft documents in coordination with the concerned department and send them for Plant Head approval.
- If available, check for the coherence of customer inspection standards, drawing with the control plan, inspection standard and operation standard and inspection reports.
- Update the Master list of documents.
- Distribute the documents to the concerned department.
Master List of documents:

CASE-II Request for Modification :
- Receive the document change request form for modification and check the implementation feasibility.
- If feasible, modify the document and prepare change points in the document.
- Take the approval of the document change request from the Plant in charge.
- Distribute the modified document to controlled copyholders. (Control copy stamp with Red color and Master copy stamp with Blue color )
- Receive old copies from controlled copyholders and destroy the old controlled copies.
- Preserve the master copy of old documents duly identified with an Obsolete stamp.
- Issue new or modified format with the implementation date.
- Collect the old format, confirm the implementation and record the change date.
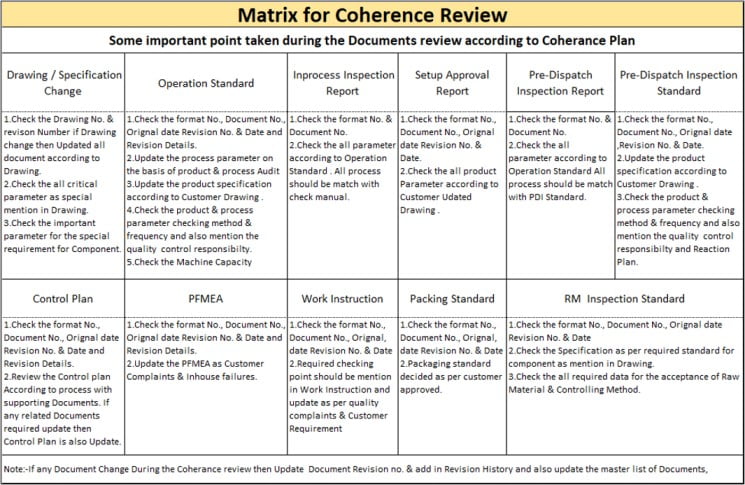
Procedure to make process control standards(QA process charts)
Do you make and review process control standards, Inspection specifications, and Operation instructions for all products that are shipped to SMC / MSIL / Tier 1?
Sub Question |
---|
Availability of documents (control plans, operation standards, inspection standards) for all parts under-supply |
Procedure for preparation and control of documents defining following: – department in charge of making, the person in charge of making, a person in charge of authorizing – revision rule & revision history (internal & customer) – Document Control Numbering – retention period; – Distribution matrix – Obsolete documents handling |
Master copies of the controlled documents |
Master list of documents (control plans, operation standard, inspection standards) with latest revision nos |
Procedure to control standards. -Process control standards -Inspection specifications -Operation instructions
Do you have the consistency to keep process control standards, inspection specifications, operation inspection and parameter chart?
Sub Question |
---|
All Product and process parameters are mentioned in the control plan |
References to WI, sample size, checking frequency, checking method, boundary samples & Poka Yoke are defined in the control plan |
Consistency among documents (process control standards/control plans, operation standards, inspection standards and customer inspection standards) |
Retention period of documents:
The retention period is the amount of time an organization keeps documents and records for audit purposes and to fulfill customer requirements.
Documents | Retention Period |
---|---|
Maru A Parts | Part Life + 11 Years |
Fit-Function | Part Life + 11 Years |
Drawing, Control Plan, PFMEA, PFD & OS | Part Life + 11 Years |
Safety and Regulatory | 5 Years |
Internal Audit and MRM | 3 Years |
Training Records | 2 Years |
Calibration Records | 2 Years |
Inspection Records | 1 Year |
Production Records | 1 Year |
Maintenance Records | 3 Years |
Equipment History Card | Equipment Life |
NPD Records | 5 Years |