As per the IATF 16949 standard, “Terms and definitions” is the third clause. Terms and definitions are used in this standard in different clauses. So below are the main terms and definitions with some simple explanations.
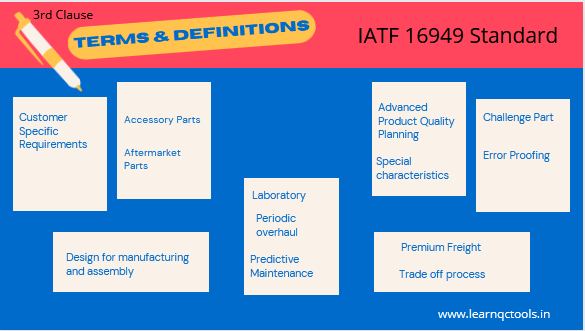
Customer-specific requirement ( CSR) :
These are the specific requirements of the customer. These can be based on the supplier quality manual provided by the customer. For example, 4M change control, packing specification, process capability requirement, countermeasure report etc. We can make a matrix for all customers and their requirements.
Control Plan:
The control plan is the documented description of the systems and processes required for controlling the manufacturing of the product. It contains Product and process parameters of all the processes from RM receipt to dispatch.
Challenge (Master) Part:
Parts of known specification, calibrated and traceable to standards, with OK or NG results that are used to validate the functionality of an error-proofing device or check the fixtures.
Accessory Part:
The customer specified additional components that are either mechanically or electronically connected to the vehicle. e.g. Wheel covers, sound system enhancements, supercharger, floor mats etc.
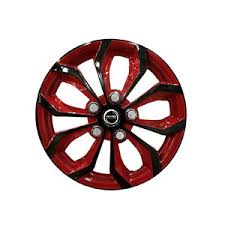
Aftermarket Parts:
These are the replacement parts not purchased or released by an OEM for service part application. These parts may or may not be produced to the original equipment specification.
Design for manufacturing and assembly (DFMA) :
It is the combination of two methodologies: Design for manufacturing (DFM) and design for assembly (DFA). DFM is the process of optimizing the design to be easier to produce. It has higher throughput and improved quality. DFA is the optimization of the design to make it easier to assemble, reduce the risk of error and lower costs.
Advanced Product Quality Planning (APQP) :
APQP serves as a guide in the development process and also a standard way to share results between organizations and their customers. APQP covers design robustness, design testing and specification compliance, process design, quality inspection standards, process capability, packaging, product testing and operator training plan etc.
Escalation Process :
It is a process used to highlight or flag specific issues within an organization so that the appropriate personnel can respond to these situations and monitor the resolution. It is also called a whistleblowing policy.
Error Proofing :
It is the product and manufacturing process design and development to prevent the manufacture of non-conforming products. It is also called the Poka-yoke.
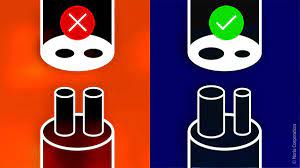
Laboratory:
Facility for inspection, test or calibration that may include but is not limited to the following: chemical, metallurgical, dimensional, physical, electrical or mechanical testing.
Laboratory Scope:
It is a document that contains a list of specific tests and calibrations that a laboratory can do. Also list of master equipment that the laboratory uses to perform the test or calibration. Also, it contains a list of methods and standards that the laboratory follows to perform the above activity.
Outsourced Process:
Outsource process is the part of an organization’s processes that are performed by an external organization. e.g. Plating, powder coating, hardening etc
Predictive Maintenance:
It is a set of techniques to check the condition of the equipment by performing periodic or continuous monitoring of equipment conditions. So that we can predict when machine maintenance should be done, in this, we can check vibration, noise, temperature and oil analysis etc.
You may like to know about the List of Mandatory Procedures as per IATF 16949.
Preventive Maintenance:
It is the maintenance of equipment as per plan (time-based) and as per the defined preventive maintenance check sheet. The purpose of preventive maintenance is to prevent the breakdown of equipment and improve OEE.
Periodic overhaul:
It is a maintenance methodology to prevent a major unplanned breakdown based on fault or interruption history. In this a part of the equipment is proactively taken out of service and disassembled, repaired, part replaced, reassembled and then returned to service.
Total Productive Maintenance :
TPM is a system of maintaining and improving the integrity of production and quality systems through machines, equipment, processes and employees that add value to the organization.
Special characteristic :
It is the classification of a product characteristic or manufacturing process parameter that can affect safety or compliance with regulations, fit, function, and performance requirements. These are as Fit, Function, Formation, Safety, Appearance and Legal.(FFFSAL)
Premium Freight :
Premium freight is the extra cost paid by the company that decided during PPAP. This can be due to method, quantity or late delivery.
Reference: IATF 16949:2016 Standard
Very useful information.
Very well addressed. Informative and self educating 👌👍
Thanks for your valuable feedback
very good
Thanks for sharing such a nice idea, piece of writing is fastidious, thats why i have read it entirely