What is Root Cause Analysis?
Root Cause Analysis is an in-depth technique for identifying the most relevant, controllable and significant cause of a problem. If we take action on that cause then the problem will not repeat due to that cause.
3 Requirements of the Root Cause:
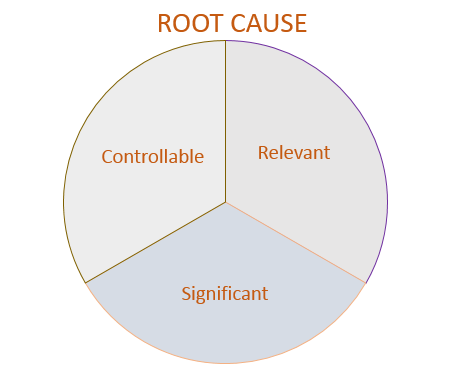
- The root cause must be relevant to the problem. If it is not relevant to the problem then it is not the root cause.
- It must be controllable. If the root cause is not controllable then it is not the root cause.
- It must be significant.
What are the 5 Whys of Root Cause Analysis?
Five whys were invented by Sakichi Toyoda in 1920. There are 2 categories for why why analysis.
Occurrence:
The first category is related to the process that made the defective part. Why did it occur? We focus on the real root cause of occurrence here. So that when we take action on the real root cause of the problem. It will not be repeated.
Detection:
The second one must address the detection system that could not detect the defective part.
- Why did the outflow happen?
- Why was it not detected in our factory?
- Why did the part go to the customer? So in this category, we focus on the second step detection.
5 Whys are not always necessary to reach the root cause of the problem. It may take less or more than 5 whys to get to the root cause. It could be 4 whys or 6 whys. It will depend upon the complexity of the problem.
Stop asking why if your common sense says you have reached the controllable step of a process, relevant document, policy or a concerned person ( operator or supervisor)
As this tool is purely observation-driven, keep asking the next why until you feel the root cause has become evident.
Useful Tools for determining Root cause analysis:
- 5 Whys
- Pareto analysis
- Brain Storming
- Flow Chart
- Cause and Effect Diagram
- Tree Diagram
Practical Examples of Root Cause Analysis :
Case Study 1 :
Problem: Flat Tyre of a Car
Why 1 | Why 2 | Why 3 | Why 4 | Why 5 | Root Cause |
---|---|---|---|---|---|
Nails on the garage floor | Nails cartoon split open | Cartoon got wet | Rain through a hole in the garage roof | Roof tiles are missing | The roof is not a part of the daily checklist |
Case Study 2:
Problem: The CNC Machine stopped
Why 1 | Why 2 | Why 3 | Why 4 | Why 5 | Root Cause |
---|---|---|---|---|---|
The overload circuit tripped | The pump was seized | Metal chips damaged the shaft | Chips entered the lubrication system | No filter on the inlet pipe | The sump design is not OK |
Case Study 3:
Problem: Rod Length under size on Band saw cutting
Why 1 | Why 2 | Why 3 | Why 4 | Why 5 | Root Cause |
---|---|---|---|---|---|
Rod movement less | Limit switch plunger not moving | Plunger jammed | Chips got into the plunger | No cover on the plunger and limit switch | Machine design not OK |
Case Study 4:
Problem: Blowhole in Aluminum casting
Why 1 | Why 2 | Why 3 | Why 4 | Why 5 | Root Cause |
---|---|---|---|---|---|
Casting filling is not OK | Molten metal does not reach the effective area | Casting ends before filling area | Casting design as per model | Design not adequate | The Gate opening design is not adequate |
Case Study 5:
Problem: Punching out in Sheet metal parts
Why 1 | Why 2 | Why 3 | Why 4 | Why 5 | Root Cause |
---|---|---|---|---|---|
Part shifted | Locator gauge shifted | Locator loose | Bolt loose | Hardened bolt not used | No checkpoint in the design for the use of hardened bolt |
Case Study 6:
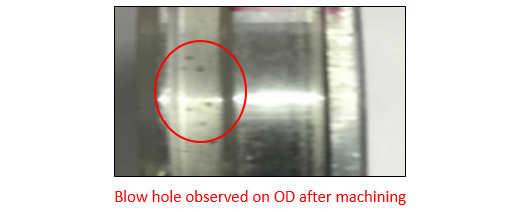
Why why for the occurrence of a Blow Hole in the Pressure die casting process due to air entraption:
Why-1 | Why is air entrapped during metal flow? |
Ans | Sleeve filling ratio more ( 55%) |
Why-2 | Sleeve filling ratio more ( 55%)? |
Ans | Effective sleeve area less |
Why-3 | Effective sleeve area less? |
Ans | Plunger dia less (50mm) |
Why-4 | Plunger dia less (50mm) ? |
Ans | As per standard practice, the die was designed according to the model and past history data are not considered |
Root Cause: As per standard practice, the die was designed according to the model and past history data are not considered
Case Study 7:
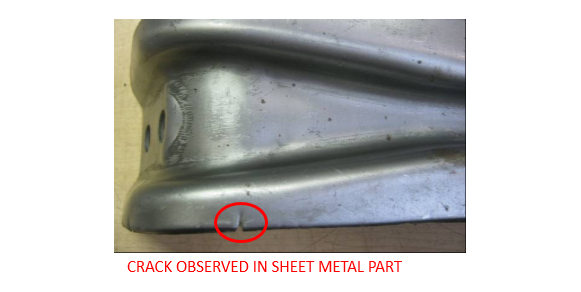
Why why analysis for the occurrence of a crack in sheet metal parts:
Why-1 | Why crack on parts after bending? |
Ans | Heavy burr on the edge of the blank |
Why-2 | Heavy burr on the edge of the blank? |
Ans | The cutting edge of the die worn out |
Why-3 | The cutting edge of the die worn out? |
Ans | Cutting edge is worn out before the defined resharpening frequency |
Why-4 | Cutting edge worn out before the defined resharpening frequency? |
Ans | Tool resharpening frequency not reviewed as per past history |
Root cause: Tool resharpening frequency should be revised as per past history.