What is OEE?
OEE (Overall Equipment Effectiveness) is a term used to measure manufacturing productivity. It is to calculate the percentage of time an equipment is truly productive. OEE is the main KPI of production to check the productivity of an equipment/plant.
For calculating the OEE of the plant or multiple machines, we can calculate by taking the average of all machines. Again, use the average method to calculate the plant’s or various machines’ OEE in a month. Seiichi Nakajima developed the concept of OEE.
3 Components of OEE :
There are three factors for calculating OEE. These are Availability, Performance and Quality. Let’s understand each one separately.
Availability:
It is the percentage of time an equipment is available for production out of the total available time. It means that if there is a stoppage in the equipment, then that will be subtracted from the total available time. Stoppage can be planned and unplanned in this category. For example, the tool setting on the machine is in the plan category. But machine breakdown is in the unplanned category.

Availability% = (Total available time – Stoppage) x 100 / Total available time
Performance:
It is the performance of the equipment as per the defined cycle time. For calculating performance, slow cycle time and small stoppages can affect.

Performance% = Production Quantity x100 / ( Net available time x Cycle Time )
Performance % can be calculated as Production quantity / Target production quantity, as per cycle time.
Quality:
It is the percentage of good quality products produced out of the total production. Good quality products are total rework and rejection subtracted from total production.

Quality% = Total OK Products x 100 / Total Production
Overall Equipment Effectiveness (OEE) calculation :
OEE is the product of Availability, Performance and Quality. OEE is calculated as a percentage.
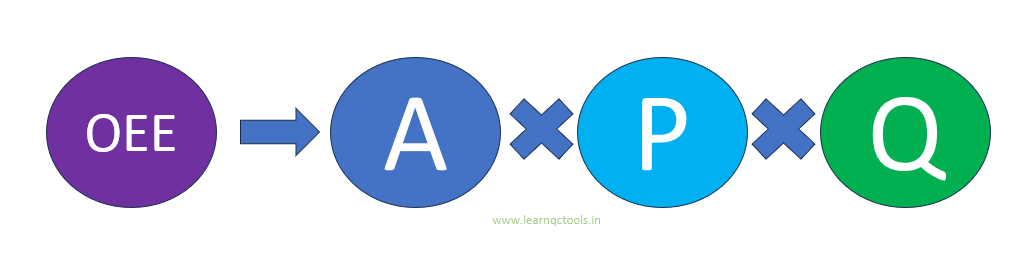

OEE % = Availability % x Performance % x Quality %
6 Big Losses:
There are 6 big losses in the manufacturing process. For calculating OEE, we have to calculate all these losses.
- Unplanned stops ( Equipment breakdown)
- Planned stops ( Setup and adjustments)
- Small stops ( Minor stops)
- Slow cycle ( Reduced speed)
- Production rejects ( Process defects)
- Startup rejects ( Reduced yields)
Availability Loss | Performance Loss | Quality Loss |
---|---|---|
1. Unplanned Stops ( Breakdown) | 3. Reduced speed | 5. Rejection & Rework |
2. Planned Stops ( Tool / Machine setup) | 4. Idling & Minor stops | 6. Setup Rejection |
Example of calculating OEE:
Calculate OEE by considering a shift of 8 hrs, Machine breakdown of 30 minutes, Total production of 3800 parts and rejection of 20 parts and the target as per cycle time is 4000 parts.
Availability = ((Total available time – Breakdown time) / Total available time) x100
Availability = ((480 – 30) / 480)*100 = (450 / 480)x100 = 93.75%
Performance = Production Quantity / ( Net available time x Cycle Time ) x 100
Performance = (3800 / 4000) x100= 95%
Quality = (Total OK Products / Total Production) x 100
Quality = (3780 / 3800) x100 = 99.47%
OEE = Availability x Performance x Quality
OEE = 93.75% x 95% x 99.47% = 88.59%
OEE Calculation Excel Sheet
Download the OEE Excel Sheet
Update the data date-wise as per the format.
OEE (Overall Equipment Effectiveness) is a lean manufacturing tool and universal best practice to monitor, evaluate and improve the effectiveness of a production process. This could be an assembly line, machine cell, packaging line etc. But it can also be considered a strong financial indicator. When expressed in monetary terms, the OEE metric can be used to illustrate the potential economic impact of optimizing production and justify investments to increase efficiency in your plant.
You may like other lean tools: Jidoka in lean manufacturing,
What is Poka Yoke (Error Proofing)?
Thanks for fantastic info I was looking for this information for my mission.