Jidoka
Jidoka is to build devices in the machines that detect defects and automatically stop the machine upon such an occurrence. When we give the power “to push buttons or pull cords” to operators is called Andon, which can bring the entire assembly line to stop.
What is the difference between Andon and Jidoka?
Jidoka | Andon |
---|---|
Jidoka is to build a mechanism in the machine that detects abnormalities | Andon is to give the responsibility to the operator to stop the machine |
It automatically stops the machine upon such an occurrence | The operator stops the machine or line by pushing the button or pulling the cord. |
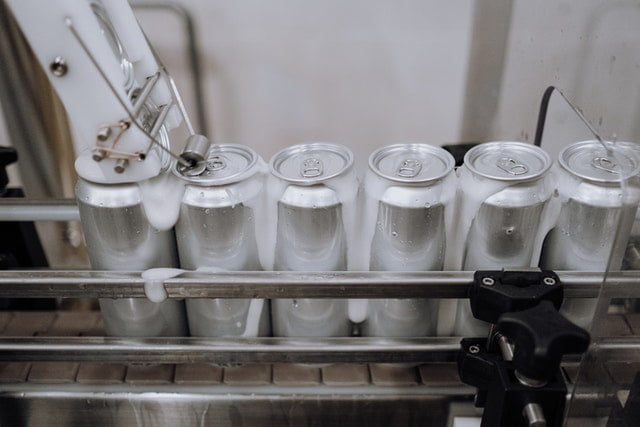
The concept of Jidoka originated in the early 1900s when Sakichi Toyoda, founder of the Toyota Group, invented a textile loom that stopped automatically when any thread broke.
Jidoka principle :
1. Autonomation:
It provides the machine the ability to stop itself when it senses an abnormality.
2. Stopping the line to remove the causes of the problem.
Stop the line and notify the problem. Never let a defect pass to the next station.
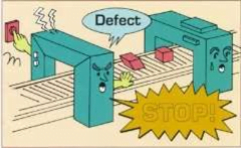
What is Autonomation :
Autonomation transfers human intelligence to automated machines so that machines can detect the production of a single defective part and immediately stop themselves while asking for help.
Jidoka uses limit switches or devices that stop a process when :
- The required number of pieces has been made.
- Any part is defective.
- The mechanism jams.
Why is Autonomation required?
- To make machines free from constant human attention.
- Operators can handle multiple machines.
Benefits of Jidoka :
- Productivity improves when operators are multi-machine handlers as compared to automation.
- Machines detect errors and stop autonomously.
- Defects and machine crashes are prevented by auto-stop.
- Errors cause machines to stop and root causes can be found quicker.
- Less internal rejection and customer-end rejection.
- As the number of breakdowns less and repair cost less.
- Provide operators the responsibility to shut down the line.
List of things for “Stop the line culture & system”:
The following list includes some things you must do to create a “Stop-the-line culture and system effectively” and how to implement Jidoka.
- Understand your current culture and why it developed.
- Create a clear vision for change.
- Pay attention to the dignity and respect of the people.
- Establish a reasonable degree of stability in processes.
- Have a method to stop the line.
- The process must provide an audible and visual indication of the exact point of the problem.
- Define rules and procedures for responding to problems.
- Teach people to solve problems.
- Increase the urgency and make it necessary to fix problems.
- Have people designated to respond when the line stops?