What is Red Bin Analysis?
Red bin analysis is to segregate and verify the defects occurring on production lines including inspection lines on a daily basis by a cross-functional team. Then understand the defects & do root cause analysis and take countermeasures as early as possible. It is a process where we do recording of previously rejected parts, do analysis with CFT & then possible corrections & corrective action are taken with target & responsibility.
It is very important to prevent the recurrence of defects and control the defects at their early stage. Red bin analysis can be done daily or weekly as per requirement. But it is better to do a red bin analysis as early as possible.
Red color bins are used to store rejections on each machine or line.
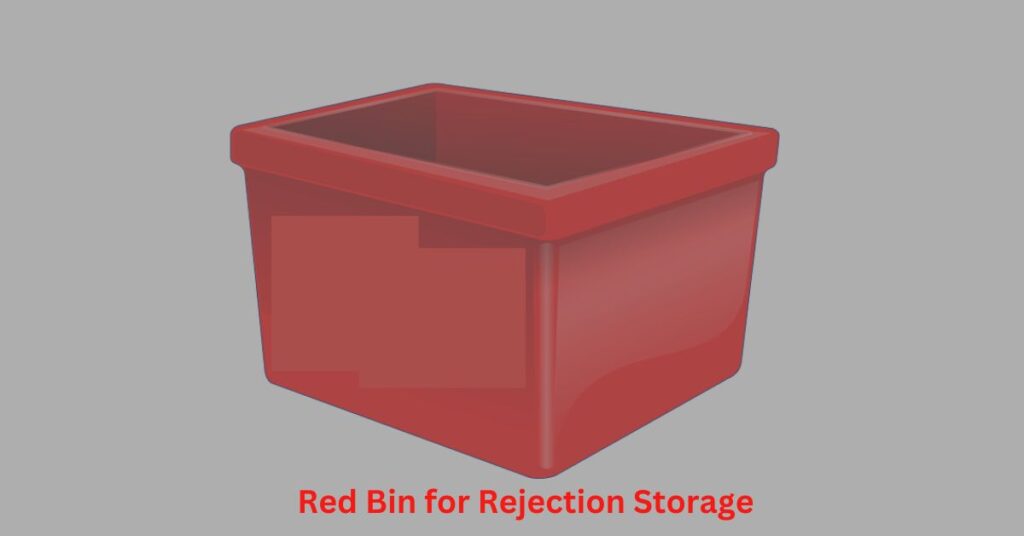
Why is Rejection Analysis important?

- If we do not do red bin meetings (analysis) on a daily basis, it will be very difficult for us to identify where to take action.
- There will be a high chance that defects can be bypassed to the customer end.
- Rejection costs will increase because no timely countermeasure action
- The cost of poor quality (COPQ) will increase.
So it is very important to do red bin meeting on daily basis & take action accordingly.
Steps of Red Bin Analysis in Quality Control :
- Put all defective parts in the red bin when detected.
- Do red marking on the defective parts for defects.
- A Red Bin should be placed near to operators in the shop.
- Put an identification tag on defective parts
- Identification tags should have information like Part name/ part number, quantity, date, shift, machine number, shop & reason for rejection etc.
- Make a CFT for the Red bin meeting with the leader.
- Make a designated area for the red bin meetings.
- Also decide the specified time for the red bin meeting.
- Also make an attendance record of the meeting.
- Carefully verify the defective parts during the red bin meeting.
- Involve operators while identifying the causes of the defect.
- Do brainstorming to identify potential causes
- Also verify the defect by visiting a place of occurrence. Follow the 3G rule.
- After doing a why analysis with the team to find out the root cause.
- Then take countermeasure action as per the actual root cause.
- Do effectiveness monitoring of the action taken.
Benefits of Red Bin analysis:
- Internal rejection reduction.
- Customer complaints reduction.
- So the Cost of poor quality is reduced.
- Corrective action is taken timely
- Customer satisfaction increase
- The cost of manufacturing reduced
- Increase in team competency
- It helps to identify where to take action
What is the use of a red bin in the assembly line?
The use of a red bin in an assembly line can vary depending on the specific context, but in general, a red bin is often used as a designated place for collecting defective or non-conforming products or components during the production process. The color red is typically used to signal the situation’s urgency and draw attention to the bin, indicating that these items require immediate attention and correction.
Having a designated place for defective items helps to ensure that they are properly separated from good items and that the assembly line can continue to operate efficiently. The red bin may also be used to track the quantity and types of defects for quality control purposes, allowing manufacturers to identify and address any recurring issues in the production process.
Why do we do red bin analysis?
Red bin analysis is a technique used to identify and eliminate waste in a manufacturing process. The term “red bin” refers to a waste bin that is designated for collecting discarded materials, scrap, and other items that are no longer needed in the process. The purpose of red bin analysis is to determine why these items are being discarded and to identify ways to prevent the waste from happening in the future. This can help improve the efficiency and profitability of the manufacturing process by reducing the number of materials and resources used, and by reducing the amount of waste produced. Red bin analysis is an important tool for Lean and Six Sigma methodologies, which are widely used in industry to improve process efficiency and eliminate waste.
Countermeasure Action :
Make a monthly summary of the red bin record. Do Pareto analysis defect-wise and then part-wise. Take action on top defects as per the Pareto chart for each section/shop. Take action as per internal QPCR criteria. It can be the top 2 or 3 defects. Also, decide the quantity for daily analysis. It can be 5 or 10 as per requirement. Find out the root cause by using a cause-and-effect diagram and why-why analysis. Countermeasure action should be implemented and results should be verified at least once a month. The countermeasure should be recorded in the red bin defect tracking sheet so that the trend can be monitored in relation to the countermeasure action taken.
Standardization & Horizontal Application :
After implementation of the countermeasure update the relevant documents & get them approved. Provide training to the concerned person. Also horizontally implement the action on a similar process or part. Also update the relevant document of a similar part or process.
Red Bin Analysis Sheet :
In the red bin analysis sheet, we do recording of rejections on a daily basis. After recording and analysis in this sheet, move all rejections to the scrap area from all the red bins. The responsible person should take action accordingly within the time period defined. The below details should be entered in the red bin analysis sheet.
- Part description ( Part name/number)
- Operation
- Rejection Qty ( Rework Qty can be added)
- Reason for rejection ( Mode )
- The root cause ( Brainstorming and why-why analysis )
- Action Plan
- Target date / Actual date (Status)
- Responsibility
Red Bin Analysis Format:
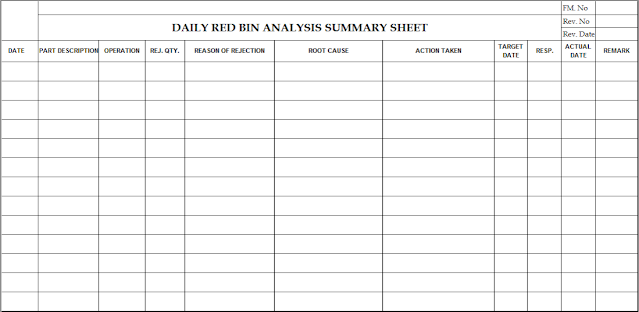
Red Bin Meeting Attendance Sheet :
In this sheet, attendance is marked off all the CFT members on a daily basis while doing red bin meetings. All members with leaders should present in the red bin meeting effectively.
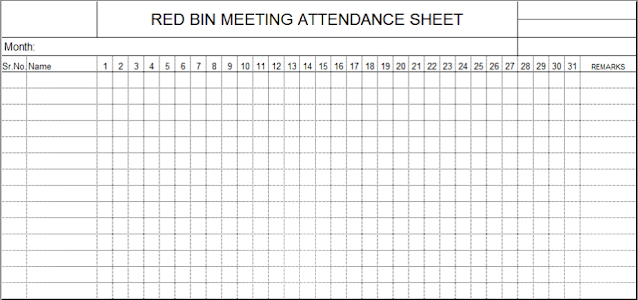
Red Bin analysis questions:
Q 1. Which color bin & tags are used for rejected parts?
Ans. a) Green b) Yellow c) Red c) Grey
Q 2. Who should be present at the time of the Red bin analysis?
Ans.
Q 3. What do you understand by the red bin area?
Ans.
Q 4. What is Corrective Action?
Ans.
Q 5. What is Preventive Action?
Ans.
Q 6. Who should be the member of the red bin analysis team?
Ans.
Q 7. Why is marking significant on rejected parts in the red bin?
Ans.
Q 8. Who is responsible for the red bin meeting?
Ans. a) Team Member b) Team Leader c) Operator d) Inspector
thank you very much
It was very useful for me