Purpose of initial supply control
Special control must be exercised during the initial phase of mass production when one of the above items occurs to collect sufficient data to judge whether the mass production can continue using the existing process. So this is the purpose of initial supply control. It is also called initial production control.
- Purpose of initial supply control
- Scope:
- Responsible for Initial Supply Control
- Initial Part:
- The flow of the Initial Part:
- Handling of Initial Part:
- Initial Supply Control:
- Initial Supply Control Scope / Category :
- Period of Initial Supply Control:
- Establishment of Initial Flow Control: Special activities:
- Information about Initial Supply Control :
- Termination Criteria:
- Initial Production Control questions as per MACE VSA check sheet:
Scope:
This procedure applies to all groups of new development products manufactured by the organization and any ECN or process change by the customer. This procedure also applies to the new BOP part/change part at the supplier end.
This is applicable for the following products, if there:-
AA – New Component: No experience in production so far.
A – Part happens to be similar to what had been produced
B – ECN:- Part happens to be a major deviation in the component that is part profile change, A New tool development and Major rectification in the tool
C – PCN: – Process parameters change (Current/ Voltage/Time/Feed/Temp/Pressure etc). Process Equipment Change
D Process sequence change/Layout Change
E- Supplier Change
F- Material Change
G- Plant Relocation
H- Sudden volume increase
I- Restart production after a long layoff (12 months)
Responsible for Initial Supply Control
The development head/quality head is responsible for initiating and terminating the initial supply control activities.
Initial Part:
Part produced during Trials, T0, T1 & Pilot lots of new product development, ECN, Process change ( PCN ) or any major change in tool/die is called the initial part.
The flow of the Initial Part:
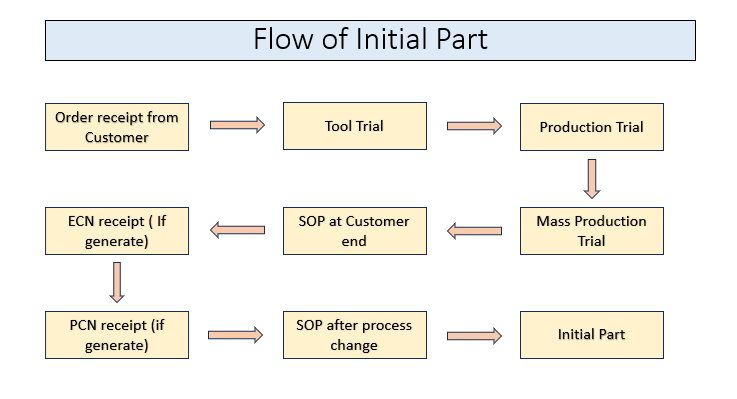
Handling of Initial Part:
Initial products are handled with extra care during the manufacturing process :
- Display identification tag on the initial part manufacturing machine.
- Put the initial part in the green color bin for the Initial Part.
- Put an identification tag on the initial part
- Prepare a report for the initial product
- Put the initial part in Lock & Key & keep only updated or recently produced parts and scrap the old parts.
- Send the initial part to the customer with an identification tag (IPP tag)
- Maintain the initial part production record
Initial Supply Control:
Initial Supply control is a process of monitoring & additional control in the process by taking precautionary & preventive actions during the initial period of mass production of a new or changed part for a defined duration. Initial supply control start date (from SOP at vendor end & end date (after completion of a period of IPC after SOP at customer end ) ”
Initial Supply Control Scope / Category :
- The new part is manufactured – New Product
- Similar to other parts manufactured – New Product
- Existing part change as per specification change required by the customer – ECN (raise)
- Start manufacturing after a long lay-off (12 months) – Process Change
- R/M, Product design/process/Tool/ Die/ Machine/ Equipment change/minor change -New Product/ECN/Process Change.
- Layout Change – Process Change
- Relocated Plant – Process Change
- Supplier / Sub supplier Change – Process Change
- High volume increase
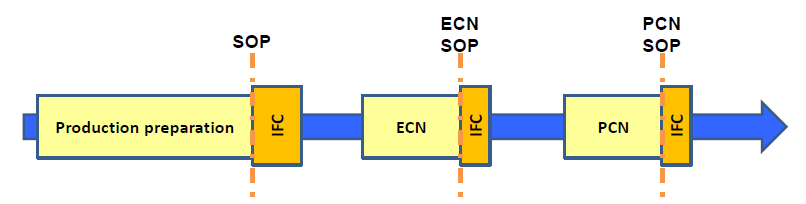
Period of Initial Supply Control:
3 Months / 5000 pcs, whichever is later for the new part.
1 Month / 1600 pcs, whichever is later for design and process change.
CATEGORY AS PER DEFINED IN SCOPE | CATEGORY AS DEFINED IN SCOPE |
---|---|
AA | 5000 pcs and 3 months |
A | 5000 pcs and 3 months |
B | 1600 pcs and 1 month |
C | 1600 pcs and 1 month |
D | 1000 pcs and 1 month for AA, A category; 15 days and 500 pcs for B, C category |
E | 1000 pcs and 1 month |
F | 1000 pcs and 1 month |
G | 1000 pcs and 1 month |
H | As per customer requirement |
I | 1000 pcs and 1 month |
Establishment of Initial Flow Control: Special activities:
The following activities related to the part (for which initial flow control is being observed) shall be carried out during this period:
- In case of a customer issue/complaint, 100% inspection is to be done for each lot qty.
- Special inspection / Process controls that are higher than normal controls. These could be either added inspection points or inspections at higher frequencies.
- Frequent Process Capability Check. It shall be carried out on special characteristics as decided by SQA or defined by the customer once a month
- Conduct an MSA once a month
- Conduct frequent Process Audits with a control plan per month during initial supply control, the first audit should be the very first day during ISC and the second audit in the middle and close all NCs within three days.
- During the ISC period, if any defect is observed, analyze the PDCA sheet.
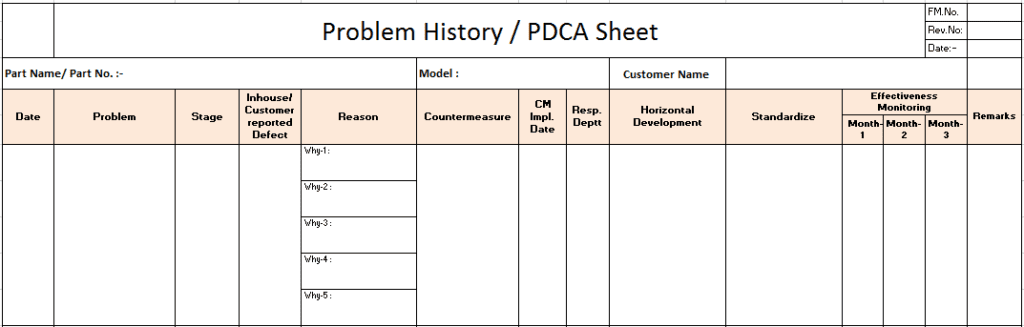
Information about Initial Supply Control :
For this Initial Supply Information Sheet is used. By this sheet, Information is provided to all the concerned persons about the start of initial supply control of the specific part. Also mention the tentative end date of the initial supply. Special control needs to be taken during initial supply control. Information can be given through any special format, any MOM or mail to all departments.
Termination Criteria:
- Customer complaints should be zero.
- Customer rejection ppm should be zero.
- In-house rejection ppm should be less than the company’s overall in-house rejection ppm. We can decide it is half of the current ppm.
- Incoming rejection should be zero.
- Process capability index (Cpk) should be more than 1.33
- Gauge R & R should be less than 10.
- Defect Rate monitoring for critical non-measurable defects
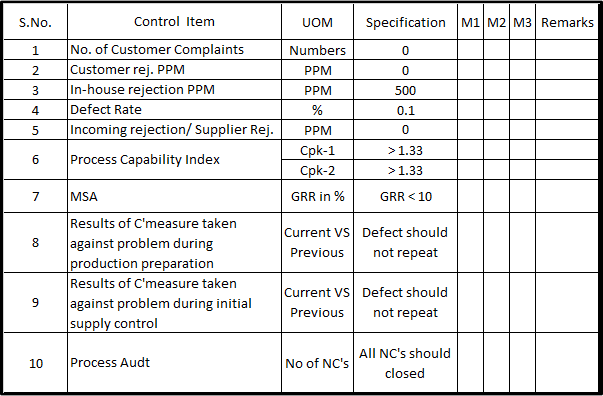
- Meeting the above target for three consecutive months and the result should have an improving trend. If not meeting the above target, the initial supply control period shall be extended until all criteria are met.
- Action to be taken in case of targets are not met.
- An action plan to improve Cpk and reduce defect rate in case of not meeting the target.
Download the Initial Supply Termination Sheet Format:
Initial Production Control questions as per MACE VSA check sheet:
2.1. Regulation for initial production control
2.1 Do you define the following items related to initial production control by standards? -controlled parts; -controlled items; -inspection method, -initial production control period, a person who announces start/end of initial production control, -finish condition.
- Scope (for new parts, part & process modifications and restart of parts after a long duration)
- Special controls (increased inspection, increased sample size etc. at all stages – incoming, in-process & final)
- Frequent process audit
- Initial production control start date (from SOP at vendor’s end) and end date (after completion of the period of IPC after SOP at customer end)
- Initial production control period
- Minimum quantity to be produced during the IPC period
- Persons responsible for the start/end
- Finish conditions (including the following): – Targets of customer complaints, rejection at the customer end, in-house rejection, supplier parts rejection, process capability, defect rate, process audit c/ms closure, effectiveness of countermeasures taken for problems reported during development and effectiveness of countermeasures taken for problems reported during initial production control.
- Meeting the above targets for 3 months for new products and as per timelines for ECN/PCN/Modification and results should have an improving trend
- Action to be taken in case targets are not met (to be extended)
2.2 How do you define items that require special control during initial production control? Do you set stricter inspection methods than ordinary inspection?
- Evidence of implementation of special controls as defined in the IPC procedure: – Increased sample size and inspection frequency (special control plan for IPC) – Process audit for verification of Standards, operation standards, facility etc. – Stricter visual inspection (100% inspection/ 200% inspection) – Stricter gauging with GO/NG gauges (100% inspection/ 200% inspection)
- Sticker targets for IPC and evidence of monthly monitoring of them
- Analysis of quality problems reported during IPC and their summary in the PDCA sheet
- Special color tags on the packing/bin/trolley on the parts produced during the initial production control period
- Termination sheet with evidence of production quantity in the IPC period and Extension of the IPC period in case the termination criteria are not met
- Evidence of communication of the start and end of IPC
2.2. Implementation of initial production control
- Identification of parameters for which the process capability study and defect rate (for critical non-measurable defects) is to be done
- Set target for Cpk (Cpk > 1.33)
- Process capability study reports (SPC)
- Defect rate monitoring record (for critical non-measurable defects)
- An action plan to improve Cpk and reduce defect rate in case of not meeting the target.
Read about:
are you on you tube, if yes please share your channel name
if no, then please start and share your knowledge on that platform also.
valuable information 🙂
Thanks for your valuable feedback. I will consider it asap.
Thanks for your feedback.
Sir,mam can you explain the process capability index with format.
Process capability index and format :https://learnqctools.in/statistical-process-control
Can someone please tell me the difference between SOP Date vs ISC
SOP Date is the Start of Production date after Pilot lot supply & approval. So it is the start date of the Initial supply control. But Initial supply control is a period for a duration of 1 month to 3 months or quantity base.
You actually make it appear really easy together with your presentation.