5S is a five-step program that is done in sequential order. 5S is a series of activities for eliminating waste that contributes to workplace rejections, mistakes and injuries. The Japanese factories are so clean that you can eat off the floor. This is simply a matter of pride for the Japanese.
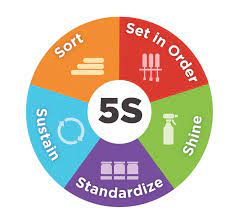
Below are the 5 Japanese words and their meaning:
1S: SEIRI, 2S: SEITON, 3S: SEISO, 4S: SEIKETSU, 5S: SHITSUKE
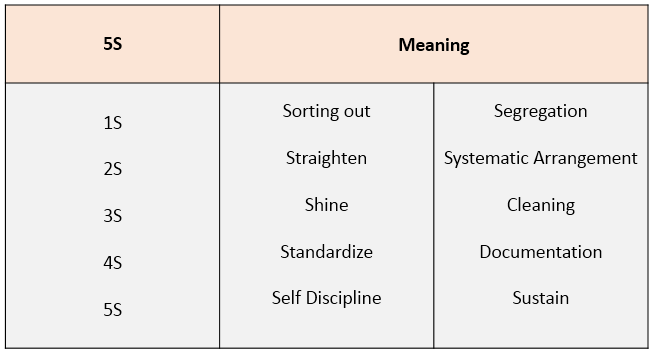
1S SEIRI ( ORGANIZATION):
To segregate all the unwanted things and eliminate them. Sorting out all the things in the workplace is the first step. Separate what is needed every day to perform the value-added work from what is not used or seldom used. Mark all unnecessary items with red tags from the workplace. Everything that moves should have a red, yellow or green tag.
Red Tag: Allocate a red tag area. Put unnecessary items there. Dispose of them at some frequency with the help of a team authorized for disposal.
2S SEITON (NEATNESS):
To arrange the necessary things in order so that they can be easily and quickly accessed. A place for everything and everything in its place. Seiton is tested by how fast you can put items away and retrieve them when needed. Every item in the factory should have a designated place. Define boundaries to identify locations and designated spaces.

3S SEISO (CLEANING):
Seiso is to keep everything neat and clean. The first cleaning will remove dirt and dust, the second will be better and the third cleaning will prepare for painting. All floors & all equipment should be painted. Cleaning should be everyone’s job belonging to his area. Everyone from the CEO to the helper should participate in the cleaning process. Decide what to clean, how to clean, who will clean and how cleaning will be done. Make 5 minutes cleaning a part of each job. This will increase ownership of the work. Display the logo as “My area my responsibility“
4S SEIKETSU (STANDARDIZATION):
To develop procedures and systems to maintain the first 3S. Standardize the daily practice of the above 3S. In this step, Visual management is focused. Once the first 3S has been implemented, focus on standardizing best practices in your work area. Standardized 5S activity charts are part of a visual factory.
5S SHITSHUKE (DISCIPLINE):
To build a habit of properly maintaining the defined procedures for continual improvement. It is the difficult part of the 5S program. Mostly in many factories, 5S activity is done for some time only. It is done during any customer audit or certification audit.
Keys to the successful implementation of 5S:
- Get everyone involved. 5S is not the responsibility of some people. But it is concerning to everyone in the company.
- Get management approval. It would be best if you had a signboard, posters etc to promote 5S activities.
- The plant Head and CEO should take 5S responsibility
- To start with, use a pilot area for the implementation of the 5S. Take photographs of the area before and after the implementation of 5S.
- Communicate the achievement. Display the before & After status of an area, and shop floor. Also communicate the benefits of 5S to everyone
Benefits of 5S implementation:
- 5S improves the safety
- Significant saving of space
- Improvement in productivity
- Reduction in manufacturing cost
- Improvement in quality
- Better working environment
- Improvement in the number of kaizens
5S Audit Check sheet:
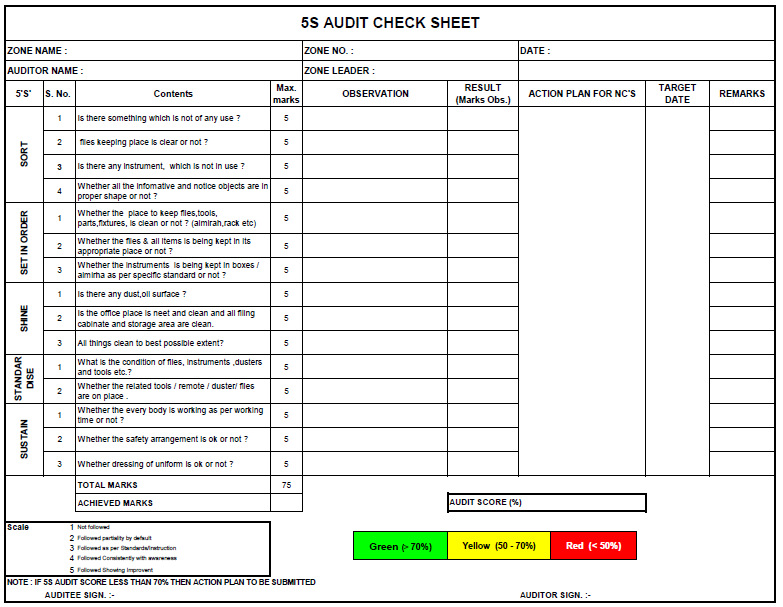
5S Management | 5S audit questions
Location of Production site:
Do you keep store material, work-in-process, finished products, inventory and containers at appropriate storage prevented from dust, rust, scratch, deformation and rainwater?
Sub Question |
---|
Condition of material in RM Store ( to be kept in covered condition away from dust, rust, scratches) |
Condition of material on the Shop floor ( to be kept in covered condition away from dust, rust and scratches) |
Condition of material in FG store ( to be kept in covered condition away from dust, rust, scratches) |
Condition of material in BOP store ( to be kept in covered condition away from dust, rust, scratches) |
Do you control material, work-in-process and finished product by designated location, volume and standard using visual control?
Sub Question |
---|
Designated area for RM material storage |
Designated area for BOP material storage |
Designated area for FG material storage |
Do you implement inspection or critical operation under a properly controlled environment luminance /temperature/humidity/vibration/noise/work table etc.)?
Sub Question |
---|
Lux value is defined and maintained as per IS Standard at Incoming, WIP and Final Inspection table and area. (minimum 500 lux for gauging, minimum 700 for visual inspection, a minimum of 300 for other areas) |
Noise level: Are the persons in High noise levels wearing PPEs? Y/N |
Monitoring of noise level in case of product quality is affected (during production or inspection) |
Condition and height of Working / Inspection table |
Production equipment management
Do you keep the condition of production equipment, jigs and tools properly?
Sub Question |
---|
The general condition of machines are proper like wiring condition, cover and dust. |
Oil/water/coolant leakage around the machine |
Tool/Jig/Fixture storage in racks |
Inspection equipment management:
Do you keep the condition of inspection equipment properly to ensure accuracy?
Sub Question |
---|
Storage of inspection equipment when not in use: in boxes or in open |
Damages of instruments |
Storage of inspection equipment when not in use: in boxes or in open |
5S Procedure
Purpose:
To ensure better material flow, visualization & no accident in the organization. Good 5S also helps in world-class quality and zero breakdowns.
Scope:
It is applicable in all areas of the organization.
Responsibility:
The overall responsibility for the implementation of this procedure lies with the production Head with the support of production supervisors.
Process description:
Description |
---|
Give awareness to operator and supervisor about 5S requirements |
Make zone map and decide zone leaders also decide Red Tag area – area to keep unwanted material |
Identify area-wise abnormalities to improve 5S as unwanted material, loose wiring, dirty machines, unidentified tools and broken / unidentified instruments and make a time-bound action plan to improve. |
Define area-wise daily checks and educate the area in charge |
Decide daily cleaning time for 10-15 minutes and perform 5S activity with the employees |
Monthly 5S audit to be conducted |
Top management shall review progress weekly |
Each Zone Leader reviews the 5S status in all areas in his zone & fills up the daily 5S Check Sheet accordingly. |
Zone Leaders monitor physical conditions, storage arrangements & proper identification of production equipment, tools & inspection equipment daily & record the verification, validation & accuracy status, as applicable, in defined formats. |
Each Zone Leader tries to achieve min. 70% passing marks. |
5S CFT conducts 5S Audits as per the Monthly 5S Audit Plan up to the 10th of The month, records status in 5S Audit Check Sheets & 5S Audit Score Card & displays the audit scores for all zones. |
If any Zone Leader gets less than 70% marks because of anything non-implemented during the audit, he conducts a Root Cause Analysis & submits it to the 5S Coordinator. |
The Zone Leader closes all nonconformities & calls 5S CFT for re-audit within 10 days of the Audit. |
He displays both scores, before & after the audit, at appropriate locations. |