Purpose:
The purpose of this machine maintenance procedure is to explain and understand the steps of attending to machines for maintenance.
Scope:
- Ensure the plant and machinery list is available and updated as of the date.
- This procedure covers the planning, monitoring & controlling of maintenance operations.
- To ensure timely inspection and safety of machines & other compliance.
- To ensure that all testing and measuring equipment available on the machines is calibrated periodically.
- Purpose:
- Scope:
- Responsibility:
- Procedure:
- Master list of machines:
- Identification of the machine:
- Preventive maintenance of machines:
- Daily machine check sheet:
- Preventive Maintenance Check Sheet Format:
- Breakdown maintenance of machines:
- Machine History Card Format in Excel:
- Predictive maintenance of machines:
- Spare parts inventory and procurement:
- Spare Part List Excel:
- Breakdown analysis:
- Breakdown Analysis Format:
- Periodic Overhauling:
- Poka Yoke (Error Proofing):
Responsibility:
The maintenance in-charge is responsible for all the activities on time.
Procedure:
Master list of machines:
- Prepare a master list of plants and machinery along with the sanctioned load of the factory if required.
- Machine location should be mentioned in the List for immediate availability of working capacity.
- Mention the machine name, machine number, make and date of installation/purchase in the list.
- The list should be updated every three months for any deletions/additions.
Identification of the machine:
- All machines should have a Unique Identification Number for easy traceability on the shop floor as machine descriptions, Make, Type, Model Number, Capacity, Installed location and Quantity etc.
- Ensure that identification is marked on each machine.
Preventive maintenance of machines:
- Ensure that all the machines’ preventive maintenance schedule is prepared.
- To ensure that preventive maintenance check sheets are defined for all the machines.
- Ensure machine preventive maintenance is done as per the schedule defined.
- If any problem is found during the preventive maintenance, the machine should be repaired in-house. If required, call the external agency without any delay and duly inform the Maintenance Head.
- If not repaired, please put a tag under maintenance.
- The work carried out is recorded in the prescribed format, like Machine PM Check Sheet & Machine History Card.
Daily machine check sheet:
It is a machine checklist in which some checkpoints are to be verified daily. The operator is responsible for updating the daily machine check sheet. This check sheet should be filled out before starting the machine. It reduces breakdown and thus increases the life of the machine.
Daily machine check sheet approved by the supervisor and filled with Judgment. If any problem is found by the operator or supervisor, then use the (x) mark and inform to maintenance department by the supervisor. Machine handover after maintenance to the production department. Maintenance records are maintained in the machine history card and the machine breakdown record.
Daily Machine Checklist Format:
Preventive Maintenance Check Sheet Format:
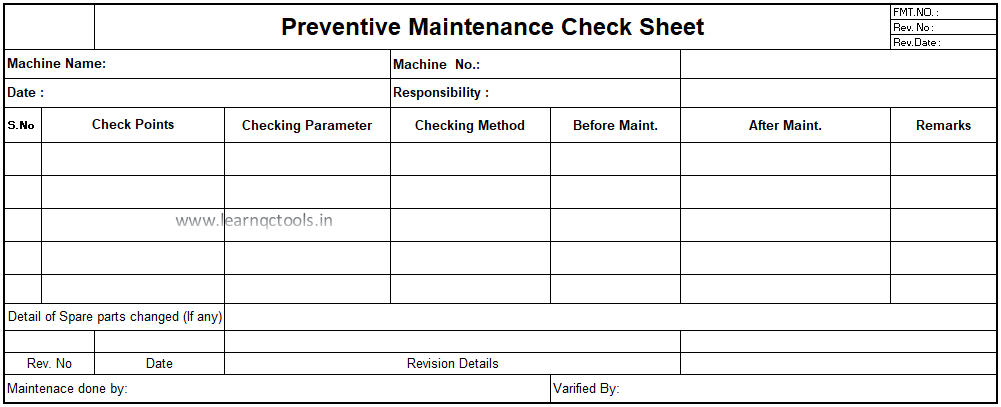
Machine Maintenance Checklist PDF:
Breakdown maintenance of machines:
- A Verbal Intimation and Breakdown Slip is made from the respective department to the Maintenance department regarding the breakdown of the machine.
- The Concerned Maintenance Shift Technician will immediately go and assess the problem. At this time, he will organize manpower to attend to the problem on a priority basis. He will communicate the expected time of completion of work. Also if more than one breakdown is to be attended, then priority is taken from HOD Maintenance in consultation with concerned departments.
- Once work is done, the trial is conducted and handed over the machine to Production after successful running. If some short-term arrangement is made to run the machine at this particular point in time due to production requirements or other reasons, then the same is communicated to Production and HOD Maintenance.
- If the problem is not rectified in-house, immediately call the external agency without any delay and duly inform the Maintenance Head.
- If the machine is repaired by an external agency, the machine service report should be taken from a service engineer.
- The work carried out is recorded in the prescribed format. Like the Machine PM Check Sheet & Machine History Card.
- 4M change record should be updated after the machine breakdown as per the 4M Change Management procedure.
Machine History Card Format:
The machine history card is used to record all the maintenance activities on the machine. All types of maintenance are recorded in the machine history card. All maintenance activities like breakdown maintenance, preventive maintenance & predictive maintenance etc. By the machine history card, we can find the maintenance history of any machine easily.
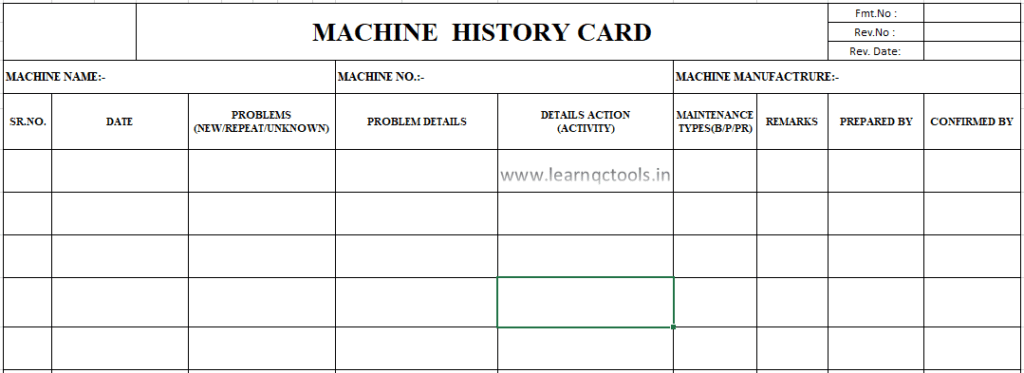
Machine History Card Format in Excel:
Predictive maintenance of machines:
- Predictive Maintenance of machines is to be planned and carried out as and when required / before failures occur.
- General techniques to be included are evaluating Vibration analysis, Sound level measures, oil analysis and other concern tests recommended by the manufacturer.
- The work carried out is recorded in a prescribed format.
Spare parts inventory and procurement:
A record is maintained for spare parts consumption and procurement is done. Minimum and maximum volume is maintained. Also define the reorder level in the spare parts monitoring sheet. Also update the spare part list on a daily basis for any shortages. If any quantity is less than the minimum quantity, then the requirement should be given to purchase for ordering.
Spare Part List Excel:
Breakdown analysis:
- Breakdown analysis is done on criteria such as Top breakdown, breakdown more than 2 hrs in a day, and repeated breakdown more than 3 times for the same problem in a month.
- Breakdown analysis is done in the prescribed format.
- Relevant documents to be updated like the daily machine check sheet, machine preventive maintenance check sheet and work instructions. A checkpoint can be added as per the corrective action taken in the check sheets.
- The effectiveness monitoring of corrective action is done for 3 months.
- Horizontal deployment to be done in a similar type of machine if required.
Note: The above breakdown analysis criteria can vary from industry to industry.
Breakdown Analysis Format:
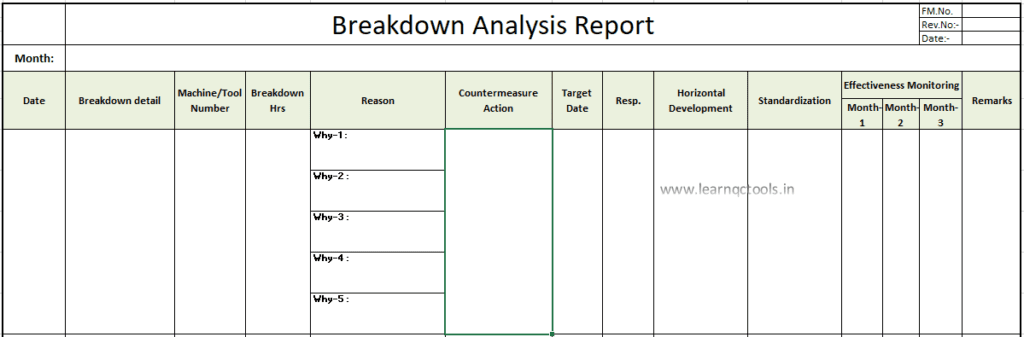
Periodic Overhauling:
Periodic overhaul is a maintenance methodology to prevent a major unplanned breakdown. Based on fault or interruption history, a piece of equipment, or a subsystem of the equipment, is proactively taken out of service and disassembled, repaired, parts replaced, reassembled, and then returned to service.
Based on breakdown history and periodic overhauling needs as desired by production, make a periodic overhauling plan for some selected equipment. Carry out periodic overhauling as per the plan and prepare the report. Provide information to the production team about the Periodic Overhauling maintenance detail one week before.
Poka Yoke (Error Proofing):
- Prepare a list of Poka-Yoke.
- Check Poka–yoke during the daily maintenance check sheet. And if any poka yoke is not checked during the daily maintenance check sheet, then check separately with a daily poka yoke check sheet if required.
- Poka yoke is also checked during preventive maintenance.
- If the poka yoke fails in the machine, then record maintain in the machine history card.
- Poka-Yoke failure analysis and CAPA submission within 3 working days.
- Production stop until poka-poke is working properly, and inform to customer immediately if required.
Nice Blog
excellent Blog. Thank sir.