“Our body is like a machine. What will happen if a regular health check-up is not done? Regular exercise not done? We may fall ill. Similarly, in the case of measuring instruments, if we do not do the proper, regular maintenance, it will also fail.” Reference the MSIL quality manual.
Types of Inspection Equipment:
Measuring Instruments:
- Micrometer,
- Vernier Caliper,
- Height Gauge,
- Bore Gauge,
- Universal Bevel Protractor,
- Torque Wrench etc.
Gauges:
- Plug Gauge,
- Snap Gauge,
- Length Gauge,
- Ring Gauge etc
Testing Equipment:
- Hardness Tester
- Plating thickness tester
- Penetration testing machine
- UTM
Accuracy Check of Inspection Equipment:
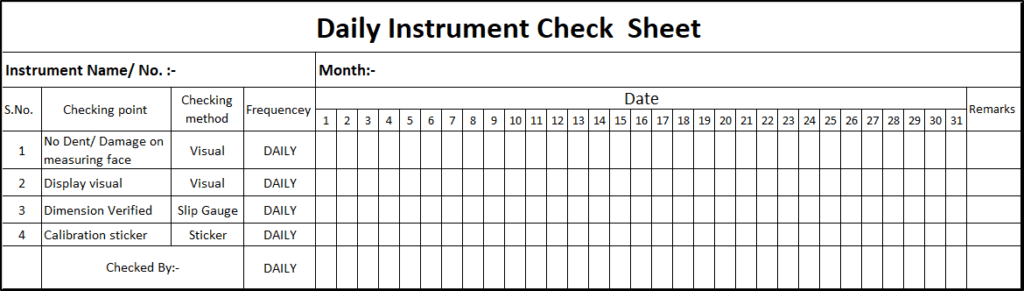
Daily/weekly periodical accuracy checks at defined frequencies shall be carried out to find out if any error in the measuring device has occurred during routine handling. Also method should be adopted to carry out daily maintenance of measuring equipment & devices.
- Daily cleaning of instruments & gauge
- Visual inspection of instruments & gauge
- Check any wear & tear of instruments & gauge
- Proper storage of instruments & gauge
Calibration of measuring instruments :
Calibration is the process of making or setting a standard ( Master ) device to ascertain & correct the accuracy of a measuring device. To properly control the calibration work & to ensure that no inspection equipment remains without calibration, it is better to follow the calibration procedure, make an annual plan for calibration & adhere to it.
Inspection standards should be prepared to specify the inspection item, judgment criteria, daily maintenance, periodic accuracy method & inspection frequency for each type of measuring instrument, gauge & testing machine.
Measuring Instruments Control:
All the inspection instruments should be identified by a unique control number. A sticker should be put on all inspection instruments with the Control Number ( Instrument ID), calibration date, & Next calibration date.
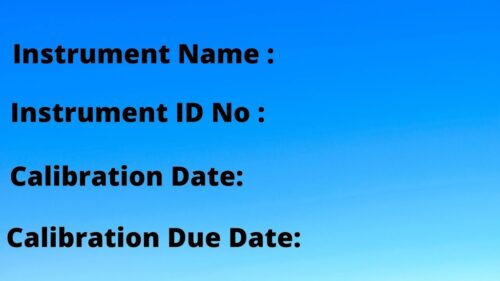
Inspection Equipment’s Registration :
A control register shall be maintained for inspection instruments with the following details:
- Name of Instruments
- Model
- Manufacturer
- Date of Purchase
- Date of installation
- Area of installation
- Control Number
- Person/shop that uses it
- Frequency of calibration
Note: If any instruments are scraped, then their control number shall not be used for the new instruments and the same needs to be captured in the control register by writing ‘Obsolete’ or ‘Scrap’.
Instruments History Cards:
Measuring equipment history cards shall be maintained, recording the events of calibration & maintenance activities respectively. Such a history card should also contain repairs or corrections made in the measuring equipment.
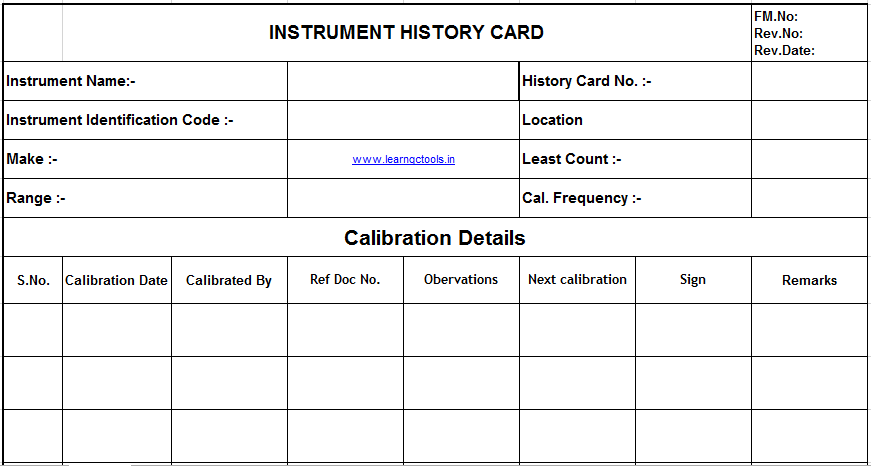
Instrument History Card PDF Download:
Measuring device out of calibration:
A documented process should be defined for action to be taken in case of measuring device is found out of calibration.
- Inform the customer if required.
- Retroactive action is to be taken on the products on which judgment has been made by using such equipment since the last calibration.
You may like to read about the Calibration Procedure
Calibration of instruments :
The accuracy & reliability of all measuring instruments would be doubtful if the instruments used were not calibrated. Calibration ensures that a measuring instrument displays an accurate and reliable value of the parameter/ dimension being measured.
The accuracy of all measuring devices degrades over time due to normal wear & tear. However, a change in accuracy can be caused by electric or mechanical shock or hazardous manufacturing equipment (oil & metal chips etc). Depending upon the type of instrument & environment in which it is being used, it may degrade very quickly or over a long period.
Frequency of Calibration :
A measuring device should be calibrated :
- According to the recommendation of the manufacturer
- After any mechanical or electrical shock
- After any excess or continuous use
- Effect of any environmental condition like temperature, humidity, dust etc.
- Periodically (Yearly, half-yearly)
Instrument Calibration Plan:
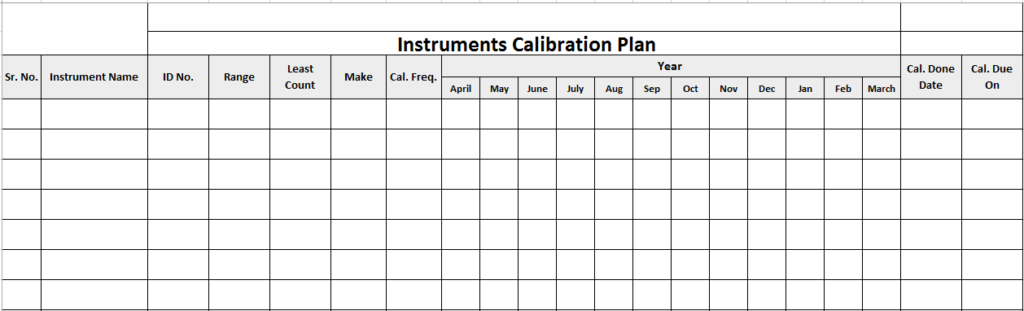
How to verify the calibration certificate?
The calibration certificate contains below information,
- Name & address of the laboratory
- A unique control number of the calibration certificate.
- Name & address of the customer
- Identification of the method & the master used with calibration details
- Description, status & identity of the calibration item
- The due date of the calibration, along with the date of calibration
- The calibration results, along with judgment criteria
- Name, designation & signature of the authorized person in charge to grant the calibration certificate with the stamp of the laboratory.
- The environmental conditions under which calibration was carried out
- NABL logo on certificate showing the scope of the laboratory & accreditation certificate issue number.
Retention Period of Calibration Record :
The retention period for the calibration record shall be a minimum of 3 years. Calibration records should be available and preserved for the specified period as per the Calibration Procedure.
nice information for maintain the measuring instruments