Purpose:
To establish and maintain a method for rework & repair of the material that can affect the quality.
Scope:
This applies to all WIP & FG stages that deviate from the actual requirement with proper deviation.
Responsibility:
QA Head is responsible for rework & repair with the support of the production in charge.
Description:
If a product deviates from its actual quality requirement, those parts must be kept separate with a Hold tag for decision.
If the decision is taken to rework, a proper deviation request must be raised detailing the problem, including the date of production, batch code, quantity, etc.
In case of a part requirement for rework, a list should be made & it should be signed by an authorized signature. It should be displayed in the rework area. Deviation should be given by HOD QA if it is not listed.
Rework will be done by the skilled operator as per the work instruction under the supervision of the QA engineer. 100% of parts are to be reverified by the QA engineer & report is to be maintained.
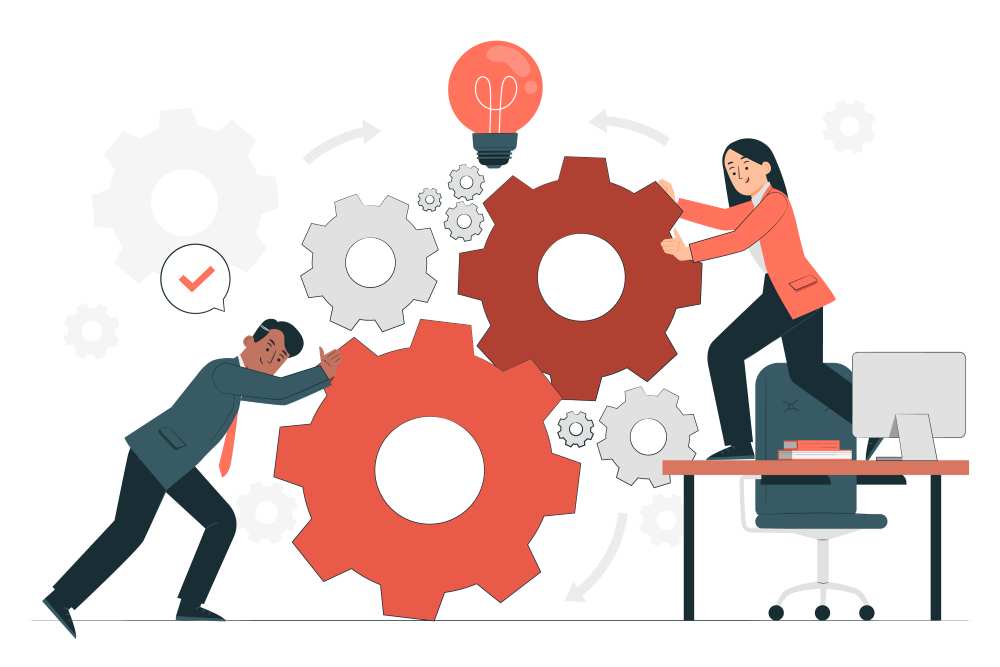
Difference between Rework & Repair:

Rework | Repair |
---|---|
Part is as per the customer drawing after rework | The Part is OK for the intended use, fitment only after repair |
There is no need for customer approval | Customer approval is required for repairing |
There is no physical change in the part after rework | There is a physical change in the part after the repair |
Example: 1. In case of a hole undersize in drilling or punching operation, the correct size hole is drilled. 2. In machining diameter is oversized, then the correct diameter is made by machining. 3. For removing small burrs in sheet metal parts. | Example: 1. In the case of porosity in welding. 2. In case of hole shift, filling by welding & then redrilling at the OK position. |
Rework Report Format:
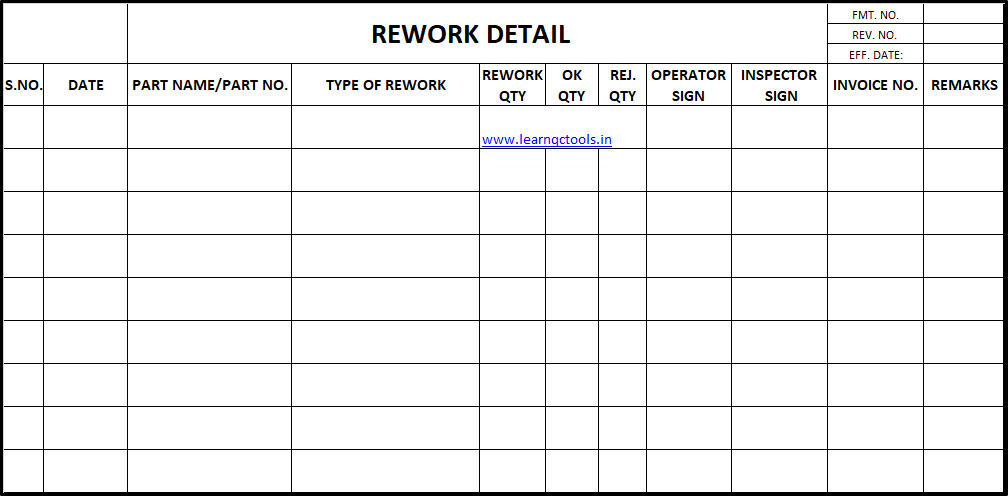
Internal Deviation Form:
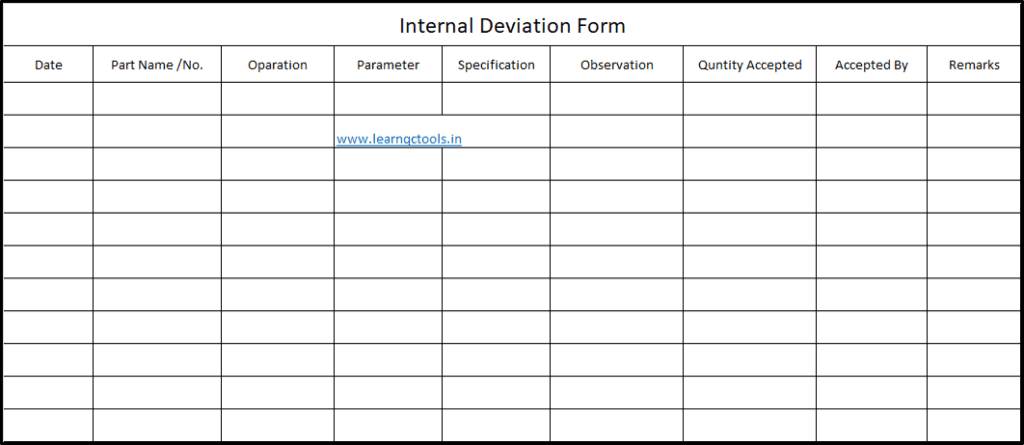
How to rework & repair for Rust, Burr, Porosity, Spatter & Nugget failure:
For the reworking of rust:
First of all, put the wire brush wheel on the bench grinder. Then, after turning on the bench grinder, clean the rust by placing the rusted part on the edge of the buffing wheel. Keep in mind that the part should not be worn excessively, otherwise the part may be rejected. After cleaning the rust, keep the reworked part in a separate bin/trolley.
For reworking of burr:
First, put the buffing wheel on the hand grinder (P 120). Then hold the hand grinder in one hand and
After turning it ON, remove the hole burr by applying the hole burr part from the burr area to the edge of the buffing wheel. Keep in mind that the part with the hole bar should not be worn excessively on the buffing wheel; otherwise, the hole may be large/oversized and the part may be rejected. After removing the hole burr, keep the reworked part in a separate bin/trolley.
For repairing porosity:
In the case of porosity / hollow welding, apply the cutting wheel on the hand grinder. Then hold the hand grinder in one hand and after turning it ON, remove the hollow welding on the part with porosity / hollow welding by applying it on the edge of the cutting wheel. Then weld the part properly by placing it in the welding jig. After welding, keep the repaired part in a separate bin/trolley.
For repairing spatter:
If the part has a MIG welding spatter, remove all the spatter from the part with the help of a chisel and hammer. Keep in mind that do not hit the rework part too hard otherwise the part may be bent/rejected. After removing the MIG welding spatter from the part, keep the reworked part in a separate bin/trolley.
For the reworking of Nugget failure:
If the nugget fails, set the parameters of the spot welding machine again and clean the dust, rust and oil from the part with the help of a cloth. Spot welding the part properly again by placing the part in the welding jig. After welding, keep the reworked part in a separate bin/trolley.
Dear sir,
Greetings of day ,
Thanks for your valuable inputs, it’s great pleasure if you share the some more defect and rework method for wledings defects .
1)Pin hole
2)Burn Through
3)Weld bead offset
4) incomplete fusion
5)excess reinforcement
6)undercut
regards
karthik M
Awesome! I thank you your input to this matter. It has been useful.
very good post, i definitely really like this excellent website, continue it
Cool article it’s really. Friend on mine has long been awaiting just for this content.
I like this weblog very much, Its a rattling nice billet to read and find info .
There are some interesting points in time in this article but I don’t know if I see all of them center to heart. There is some validity but I will take hold opinion until I look into it further. Good article , thanks and we want more! Added to FeedBurner as well…
I’ve recently started a site, and the information you offer on this website has helped me greatly. Thank you for all of your time & work.
I genuinely enjoy examining on this web site , it has got great posts .
Your blog is one of the better blogs I’ve came across in months. Thank you for your posts and all the best with your work and blog. Looking forward to reading new entries!