Sheet metal parts are the parts that are produced by stamping operation by sheet metals. During stamping operation, there are many sheet metal parts defects such as burrs, dents, scratches, wrinkles, fractures, cracks & wrong dimensions etc. So below are the operation-wise defects, their causes & remedies.
These are the defects that increase internal rejections. An increase in internal rejection increases the cost of poor quality. So root cause and action below will help in rejection analysis during red bin analysis.
Sheet metal defects and remedies:
Punching, Blanking and trimming operations:
Defect: Burr on blank or punching parts
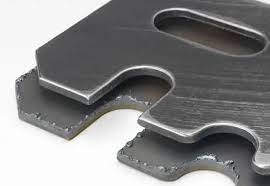
Causes | Remedies |
---|---|
Cutting edge blunt | Do grinding of punch & die face |
More clearance between the die & punch | Maintain adequate clearance |
The punch position shifted as per die | Maintain uniform clearance between die & punch |
The top of the tool shifted from its bottom | Replace guide post or pillar bush |
Die part shifted | Set the die part in the socket & use the dowel pin |
Draw operation:
Defect: Wrinkle
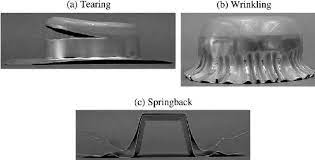
Causes | Remedies |
---|---|
The wrong lubricant used | Change the lubricant |
Blank holding pressure low | Increase the blank-holding pressure |
Defect: Fractured Rim & bottom in the draw
Cause | Remedy |
---|---|
Blank holding pressure too high | Reduce the pressure |
Punching Operation:
Defect: Dent on cutting edge
Cause | Remedy |
---|---|
More play of posts in bushings | Replace bushings |
Cutting element shifted | Maintain uniform clearance in die & punch |
Press slide not parallel with the bed surface | Repair the press |
Tool shoes not parallel ( Spacer below tool) | Grind the shoes |
Blanking operation:
Defects: Press jerks when blanking:
Cause | Remedy |
---|---|
Cutting force too large No taper on die cutting-edge | Grind die face & make taper on die cutting edge |
Defect: Stripper fails to remove stocks:
Cause | Remedy |
---|---|
Spring too weak | Replace spring |
Bending & Forming operation:
Defect: Wrong dimension:
Cause | Remedy |
---|---|
Locator worn out | Repair or replace the locator |
Locator shifted | Rectify the locator position |
The Workpiece shifted as the operation starts | Make provision for blank holding |
Spring back | Change the tool working part to allow the spring back |
I’m extremely impressed along with your writing abilities and also with the layout on your weblog. Is that this a paid theme or did you modify it your self? Either way stay up the nice quality writing, it’s rare to peer a nice weblog like this one today.
Ernestopro.com offers comprehensive solutions that effectively address various sheet metal defects in manufacturing. Their expertise ensures quality control and defect prevention throughout the process, making them an invaluable resource for anyone looking to improve their manufacturing outcomes. I highly recommend ernestopro.com for reliable assistance in resolving sheet metal issues efficiently.