Process Scope:
This process is applicable to establish a system for the identification and disposition of non conforming products at all stages i.e., Incoming, In-process, Finished stages and Customer return.
Process Owner:
HOD Quality
Process Description:
Process to control Incoming Rejection:
Non-conforming Products at all stages (incoming, in-process & final) shall be identified with a tag & segregated from the production area and shall be kept in a special location to prevent its inadvertent use.
Non-conforming material received at the incoming stage shall be disposed off as follows:
- Rejected and sent back to supplier.
- If incoming material segregation is required then the material is put in the rejection area in the store department.
- Rework by Supplier.
- Accepted with deviation if approved by the customer.
- Reject material collected from the final inspection area.
- If the material is rejected, then talk to the supplier that your material is rejected and send the material back and if there is a need to take deviation in the material, then talk to the customer and keep the material in the rejection area, put a red tag on the material. If the customer gives the OK to the material, then he will put the material back in the OK area, and if the customer rejects it, he will apply red paint to the material and inform the supplier and return it.
- If supplier rejection is found during production, then stop the production and inform the supplier.
- The supplier will check the part and keep the rejected material separately, reject the material back to the supplier and will process the OK material.
CAPA raising criteria for a supplier:
- The customer line stopped due to the supplier’s material.
- Raised DCR (Defect countermeasure report) for critical defects (Low hardness, Crack, Material burnt during plating etc)
- More than 03 Nos of the same defect were found during the incoming inspection.
- If less than 03 Nos of the same defective material. Hold the material and inform to supplier for segregation.
Action Plan from Supplier:
- Submit CAPA by the supplier within 07 working days or as per customer requirement.
- If the material is found low hardness and crack then CAPA is submitted within 03 working days.
- On-site verification after submission of CAPA will be verified within 07 working days, based on the final documents.
- During verification, if any non-observation is found then advised suggestion and closer report submitted by the supplier within 03 working days.
Process to control Inhouse Rejection:
- If the operator detects any non-conforming product during Production, he will inform to HOD (Production) / Supervisor & Mark with red paint and put it in a red bin.
- Non-conforming products are noted in the Non-Conforming Product Record (Red bin analysis)
- At the end of the shift, all NC products produced by machine /final inspection area /suspected areas collected by the Line inspector.
- Reject part put in red bin area and record maintained in red bin register.
- Non-conforming products are reviewed by CFT to determine:
- Accepted with or without rework by concession.
- Rejected or scrapped.
- Rework records maintained by the CFT Team
- Do a Red Bin Analysis for all rejected parts of the previous day at a defined time and take necessary action with the help of CFT.
- While doing Red Bin analysis, if the related team needs training then give them training and get them signed in the Red Bin record.
After analysis make a scrap note of rejected parts and get it approved by Top Management.
Where considered appropriate, the QA Head may obtain concession/deviation from the customer for further action.
Process to control Suspected Lot:
A suspected lot is a lot that may be OK or may not be. This lot must be treated as a non-conforming product. For example, if an operator/inspector is in doubt that some rejected parts are mixed with an OK lot then this lot will be treated as a suspected lot. Then this whole lot will kept separately with identification. The lot is required for 100% inspection for all parameters as per inspection standards by the concerned person. Recording of inspection will be done as per the sampling plan. If all are OK then it will be taken with the OK lot.
- Any non-conforming products detected shall be offered by Production to the QA Department for rechecking / re-inspection & disposition.
- Material is collected from suspected areas daily recorded and maintained in a red bin register and analyzed daily.
Analysis & Corrective and Preventive Action of Non-Conformity:
The analysis shall be done, using any problem-solving techniques. A record of the analysis shall be maintained. Corrective action shall be taken based on the result of the root cause analysis.
Criteria for analysis through DCR:
- Raise DCR if Number of Rejection Qty of a single part for a single defect in the same day will cross by 10 parts. (Defect Countermeasure Report)
- Raised DCR for critical defect (Low hardness, Crack, Thread Profile is not match )
- Criteria are to be revised every 6 months based on previous results.
- Rejection PPM Target 10% reduction based on the current PPM target. If the current rejection PPM observed is below to target PPM (during 06 six-month rejection PPM is maximum as per the defined target then there will be no change PPM target in the next 06 months.)
- Raised DCR if the number of rejection qty is more than 10 Nos in the single part for a single defect in the same day found in the final inspection area.
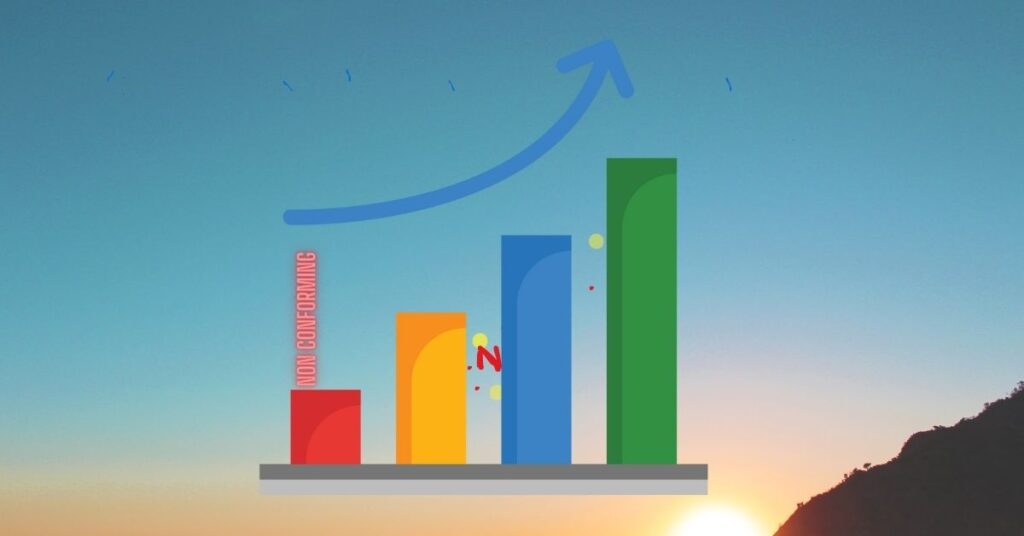
In case any non-conformity is known after dispatch to the Customer, immediate intimation shall be sent, based on discussion with the concerned representative; a decision shall be taken for its disposal. Details shall be recorded in “DCR”
Prevention of reoccurrence:
Appropriate Corrective/ Preventive steps shall be initiated to minimize/ prevent the re-occurrence of the non-conformance based on the criticality of the nonconformance, frequency of occurrence etc.
Every month part-wise Pareto takes the top defective part and analyzes the top defect. Select the top defective part after that raises the DCR of the top defect of 01 part and makes Pareto.
(The Pareto Chart is made part-wise, in the part-wise Pareto chart the most defective part is selected)
The part which has the most defective part is made defect-wise Pareto.
Let’s see which type of defect is maximum in defect wise Pareto chart.
DCR prepared the top defect of the defective part. Note:- If the top defect quantity equals more than one defect then select the most possibility which is produced during does not aware of operator, machine etc.
Review/standardization of the all concerned doc. Like PFMEA, Control Plan, Operation standard, Daily Machine check sheet etc. after implementation the corrective and preventive action.
Review all other processes and parts where these corrective actions and Preventive actions are horizontally deployed. Horizontal Deployment after 03-month analysis effectiveness monitoring is effective.
Check the effectiveness of countermeasures till the next three months. If after effectiveness monitoring PPM is 1/3 of the defined target or 1/3 observation months of the PPM then action is controlled or taken other action and effectiveness monitoring in the next three months.
Maintain the summary of all in-house raised DCR in the summary Register. On-site verification will be done after the submission of DCR.
All Raised DCR must be submitted within one week of its raising and corrective action must be taken within 10 days. Every month, the DCR analysis will be done first week of next month.
Rework Record and Analysis:
Rework material collected from the machine, final inspection area, red bin area, return from customer end and record maintained in rework & Segregation register.
Material is reworked manually or by machining, and then the record is maintained in the rework & Segregation register.
- Material reworked by defined CFT Team.
- Material to be reworked by a minimum level-3 operator and defined CFT Team.
- Material reworked as per defined Work instruction.
- Rework material trace by invoice number.
- After reworking if the material is found OK then send in the final inspection area, and if the material is found rejected then the record is maintained in the red bin register and analyzed as per the requirement
- During NPD and IPC/IFM, the part does not allow for rework.
NPD Part handling during Rework/Repair process:
During NPD Time and IPC/IFM duration rework or repair is not allowed. If any situation customer approved during the customer feasibility study then the part is reworked and the record is maintained and informed to the customer.
Read about the Procedure for Customer Complaint Handling