The Seven Quality Control (QC) tools are graphical techniques for identifying and solving problems in manufacturing and other industries. Below are the benefits of each of the 7QC tools separately:
Benefits of Flowcharts:
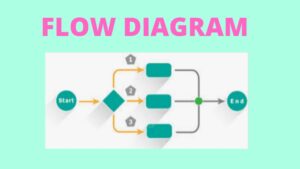
- Flowcharts are diagrams that visually represent the steps in a process.
- Flowcharts are used to map out and understand a process, identify bottlenecks and inefficiencies, and improve process flow.
- They can also be used to document and communicate processes within a company, making it easier for employees to understand and follow standard procedures.
Benefits of check sheets:
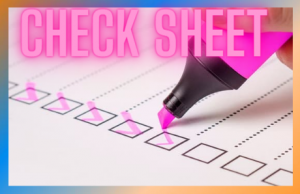
- Check sheets are tools used to collect data systematically.
- They can be used to record the number of defects, count the number of units produced, or track the time it takes to complete a task.
- By collecting data in a structured way, check sheets make it easier to identify patterns and trends and to make data-driven decisions about process improvements.
You may like to read about the Check Sheets
Benefits of Pareto charts:
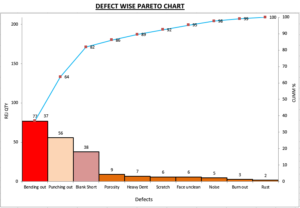
- Pareto charts are used to identify the most important problems.
- They are based on the Pareto principle, which states that 80% of the effects come from 20% of the causes.
- Pareto charts are used to identify the most significant issues that are causing the majority of problems in a process.
- By focusing on the most important issues, organizations can get the most bang for their buck when making improvements.
You may like to read more about Pareto Charts
Benefits of Control charts:
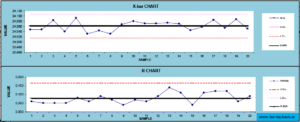
- Control charts are used to monitor process performance over time.
- They help identify patterns and trends in data and are used to detect special causes of variation in a process.
- Control charts are used to identify when a process is in control and when it is not by identifying when a process is not in control, organizations can take corrective action to bring the process back into control.
Benefits of Histograms:
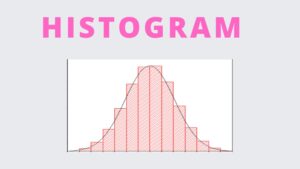
- Histograms are used to display the distribution of a process variable.
- They are used to show how data is spread across a range of values.
- Histograms can be used to identify patterns and trends in data, and can be used to detect changes in the distribution of a process variable over time.
- By identifying patterns and trends in data, organizations can make data-driven decisions about process improvements.
You may like to read about SPC, Control Charts and Histogram
Benefits of Scatter diagrams:
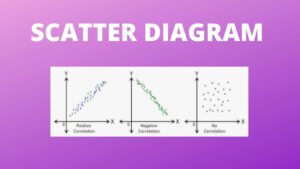
- Scatter diagrams are used to identify relationships between variables. They are used to show the relationship between two variables, such as the relationship between the number of defects and the number of units produced.
- Scatter diagrams can be used to identify patterns and trends in data and can be used to detect changes in the relationship between variables over time.
- By identifying patterns and trends in data, organizations can make data-driven decisions about process improvements.
You may like to read more about the Scatter Diagram
Benefits of Cause-and-effect diagrams:
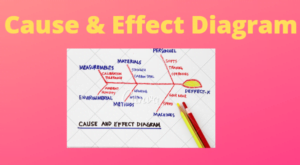
- Cause-and-effect diagrams, also known as Ishikawa diagrams or fishbone diagrams, are used to identify the root cause of a problem.
- They are used to identify the causes of a problem by breaking it down into smaller components and then identifying the underlying causes of each component.
- Cause-and-effect diagrams can be used to identify patterns and trends in data and can be used to detect changes in the underlying causes of a problem over time.
- By identifying the root cause of a problem, organizations can take corrective action to prevent the problem from happening again.
You may like to read more about the Cause and Effect Diagram
In summary, the benefits of using these tools in a manufacturing industry include:
- Better understanding and communication of processes,
- Improved process efficiency and effectiveness,
- Reduced defects and rework,
- Increased customer satisfaction,
- Improved product quality,
- Increased productivity,
- Reduced costs,
- Improved decision-making, and
- Improved employee morale and motivation.
You may like to read more about Process Flow Diagram